▲許多頂尖超跑的內外車體結構性零件都是採用碳纖維材質所打造,其中的製作技術層次已大大超越一般改裝部品的領域,是真正的高科技賽車產物。
問題六:碳纖維鈑件聽說還有分等級?
可分成「手積層」、「真空抽吸」與「熱壓成型」三種類。
最吸引人的輕量化車體鈑件,莫過於採用Carbon碳纖維材質打造的部品,外觀最大特色就是清晰可見的立體纖維,碳纖維會被當成許多賽車或高科技的應用品,最主要的原因在於相同面積下,能擁有比其他材質(鋁合金或鋼等)還要高的強度及更輕的重量,而且藉由編織手法的不同,還能創造出不同的強度及韌性,但碳纖維最大的缺點就是成本相當高,當然也反映在售價上,一塊全碳纖維引擎蓋單價往往超過3萬以上,營造出高不可攀的性能象徵。不過大家是否知道,同樣是擁有碳纖維紋路的空力套件,底子裡的製程若不同,特性與重量可是天差地別。
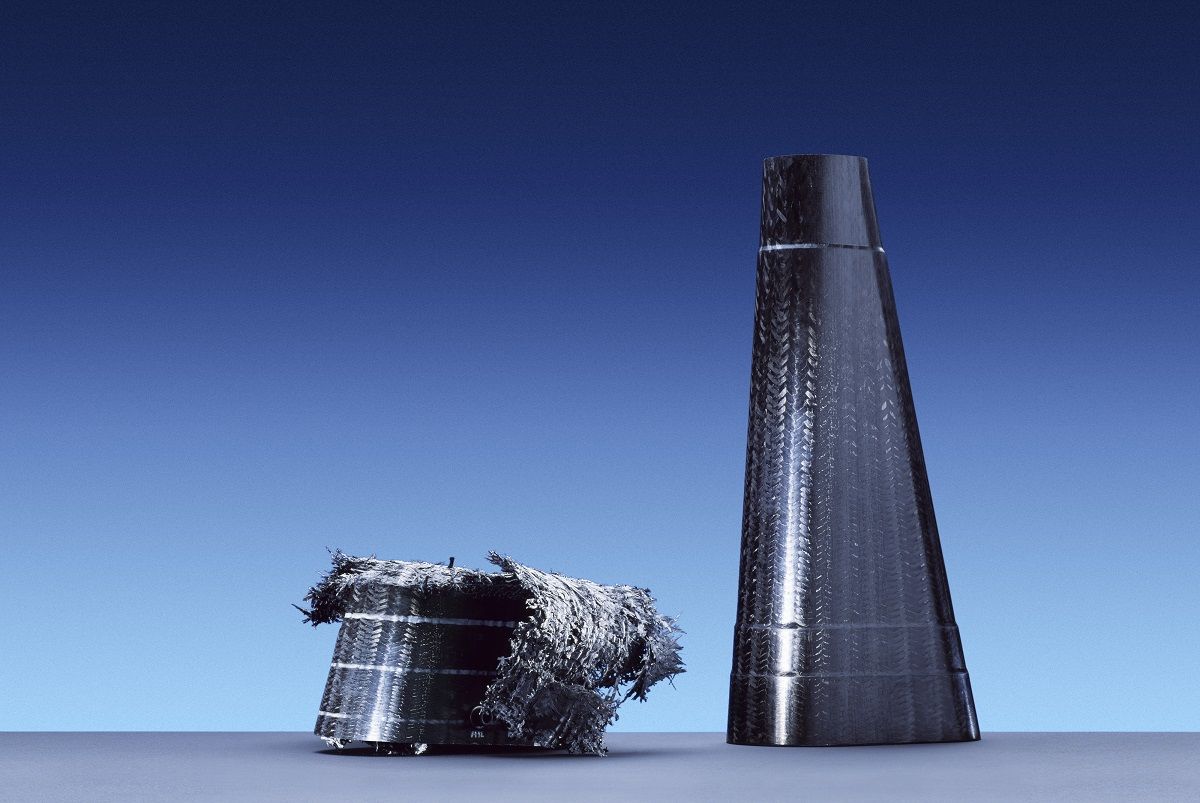
碳纖維之所以會被大量使用於賽車上,除其擁有輕量化效果外,硬度與抗衝擊的能力也是關鍵之一,圖中的碳纖維錐狀物經過撞擊後,並不會整個碎裂,而是呈現網狀破損,代表碳纖維可有效吸收撞擊力道。
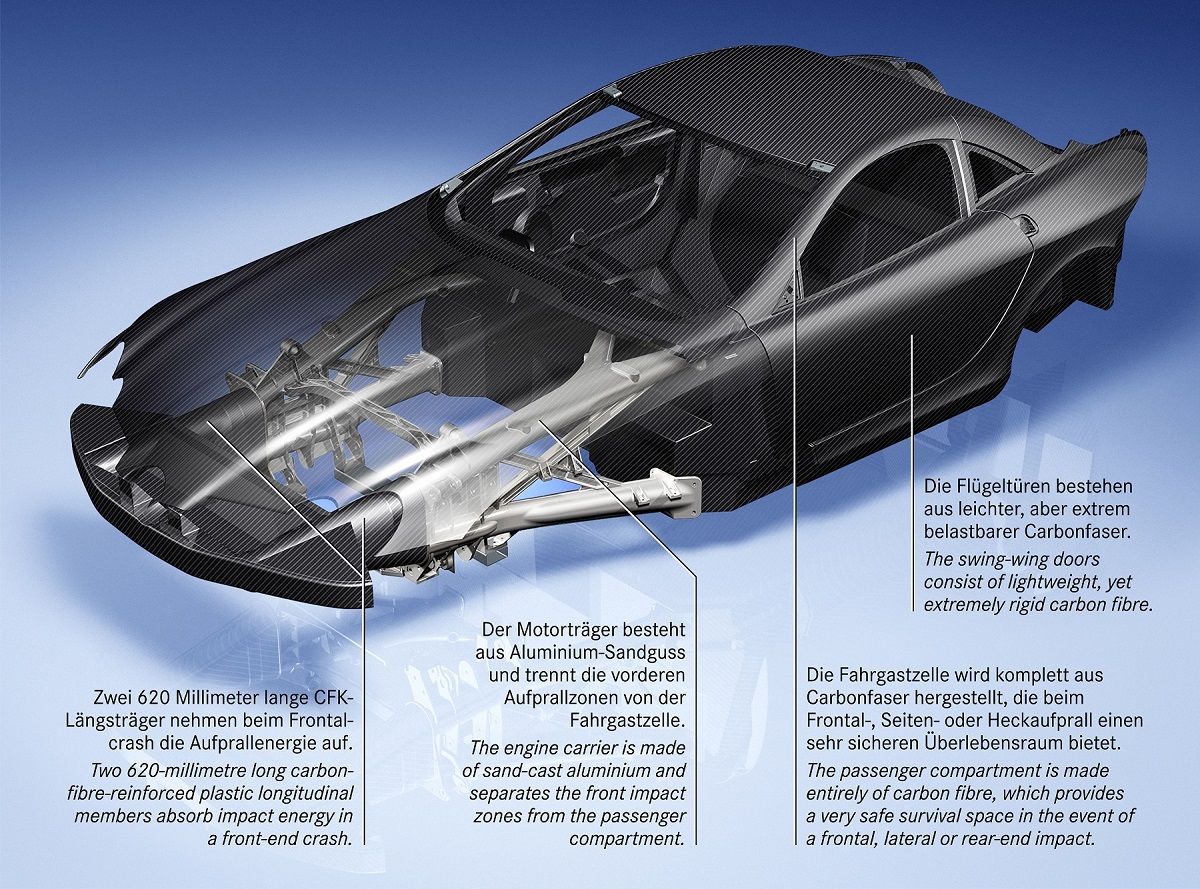
許多頂尖超跑的內外車體結構性零件都是採用碳纖維材質所打造,其中的製作技術層次已大大超越一般改裝部品的領域,是真正的高科技賽車產物。
不過同樣是碳纖維空力套件,其實依照製程方式,還可分成「手積層」、「真空抽吸」與「熱壓成型」三個種類。其中「手積層」工法是最低階的製程,此方式也是目前改裝用碳纖維產品的主要製程,所佔比例相當高,製造時只須有「外模具」,目的在塑造產品外型曲線,先把以手工方式將玻璃纖維一層層黏貼於模具上以建立強度,乾燥後再從模具中取出,進行表面碳纖維布的披覆、上金油與研磨工作,此工法製成的產品優點在於生產成本低,技術力不高,因此產品售價比較能讓人接受,仍是汽車改裝市場上的主力。缺點是耐熱性差、又厚且重,產品精密度低,而內層為玻璃纖維,不只光滑度不佳,且由於碳纖維只在外層具美觀效果而已,並不能算是真正的碳纖維製品,重量無法減經太多,輕量化效果難以跟高階的碳纖維製品相比擬。
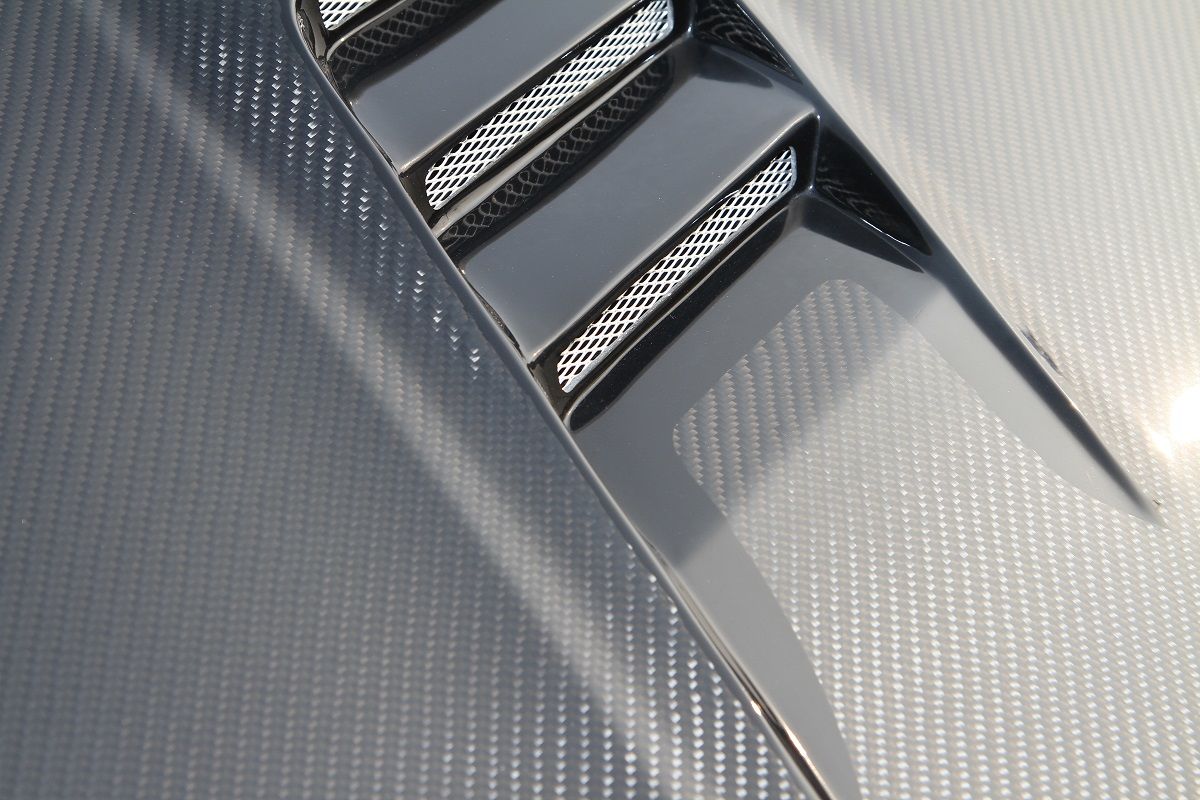
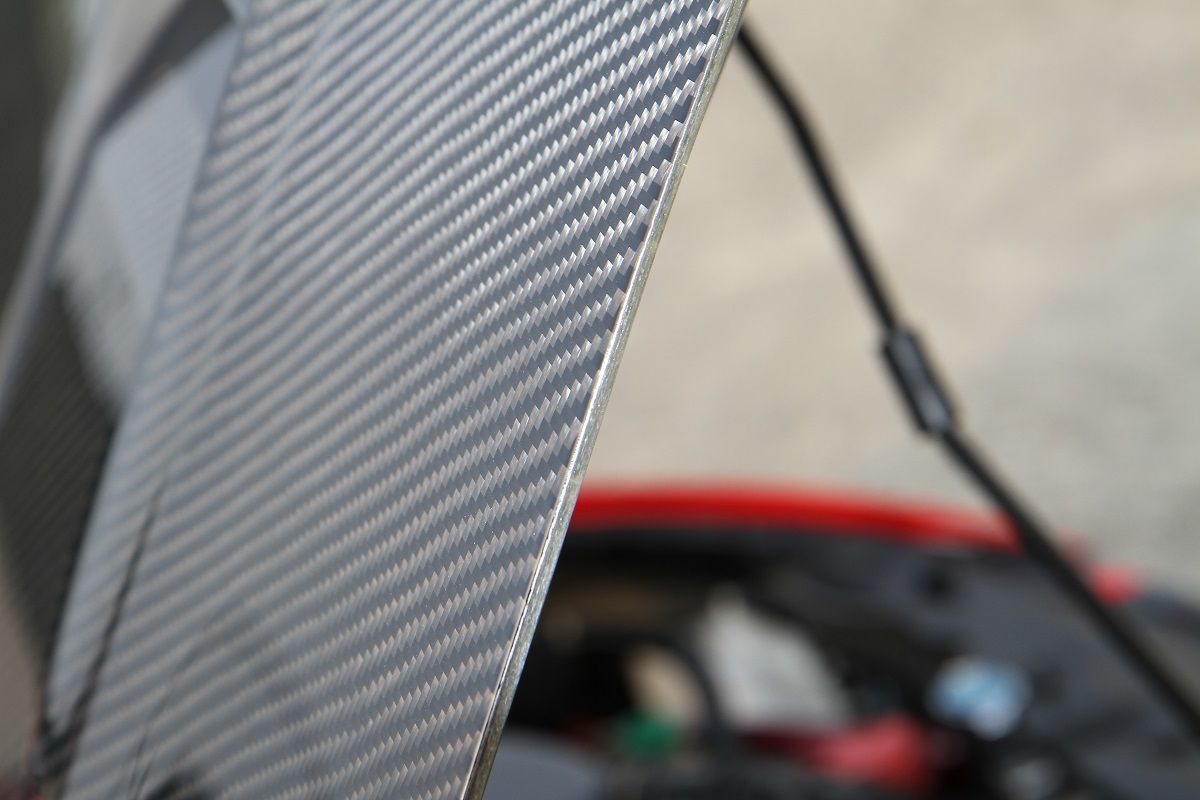
這張碳纖維引擎蓋就是熱壓成型工法所打造,因此背面仍可見玻璃纖維的紋路,且從切面來看,可明顯看出中間為半透明的樹脂層,表面散熱孔還可見黑色未批覆碳纖維布的地方。
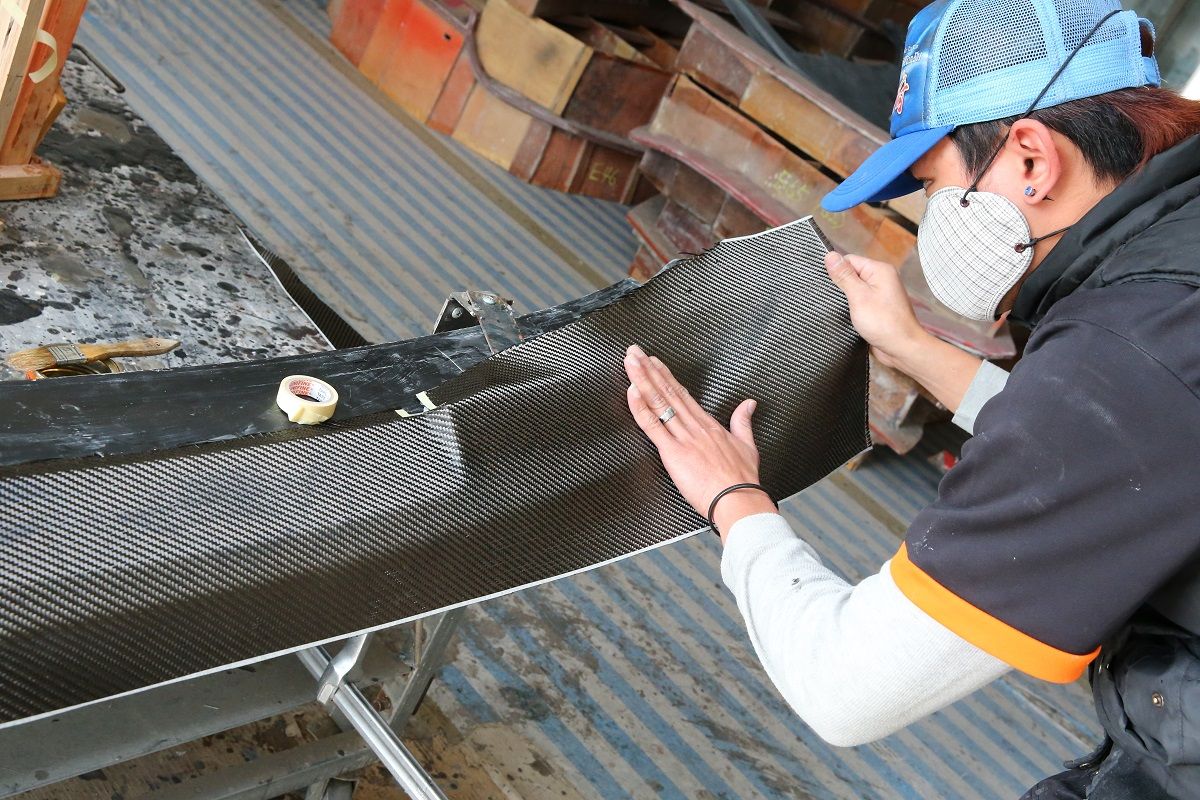
「手積層」碳纖維製造工法是在FRP部品表面,再貼上一層碳纖維布,並進行上金油與研磨工作,因此底子裡還是FRP的材質,重量並無法減輕太多,且整體硬度遇熱偏軟,尤其是引擎蓋更為明顯。
問題七:如果碳纖維體積不小,但卻需要精密尺寸的話,有哪個方法是可以兼具成本與產品質量的呢?
碳纖維成本與品質均衡點-真空抽吸工法
筆者過去在採訪時也曾遇過有些進氣集氣箱,是採用上下盒組立而成,體積也不小且結構複雜,看起來應該很難使用「手積層」或「熱壓成型」來製造,因此後來又有廠商研發出所謂的「真空抽吸加壓」工法。
這樣製程中同樣需要「內外模具」,只是模具不需金屬模,外模一樣是塑型用,內模則是加壓用,製造時會先在外模上鋪設碳纖維布,之後套入內模,內模上有許多條管子,其中一條管子是用來抽吸內外模間的空氣,兩個模具間是無法讓空氣進入,因此內模將會緊緊壓住碳纖維材質與外模,另一條連接黏著用的樹脂,開始抽吸真空時,環氧樹脂會因此被吸入模具中,待樹脂流到另一條導流管時,表示模具已被樹脂填滿,且成型時還會加熱內外模具,目的在穩定環氧樹脂的性質,並提高產品製成後的耐高溫與耐撞擊能力,等樹脂乾燥之後,再行脫模完成打模、修補、噴金油等後續加工。
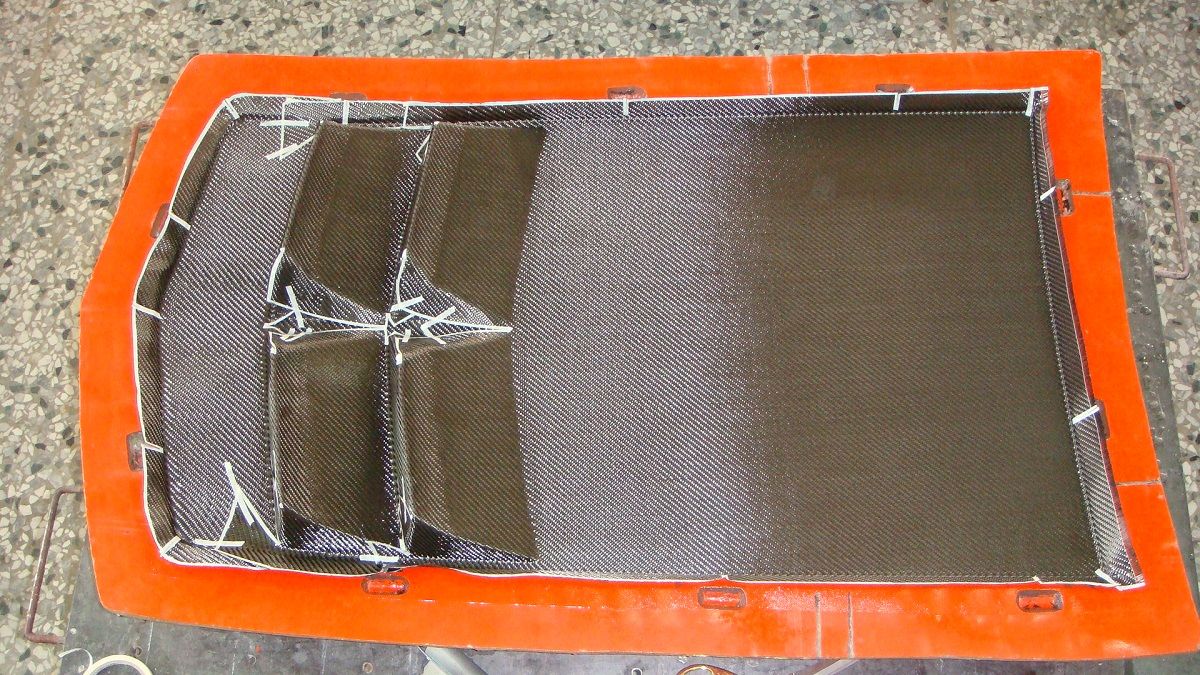
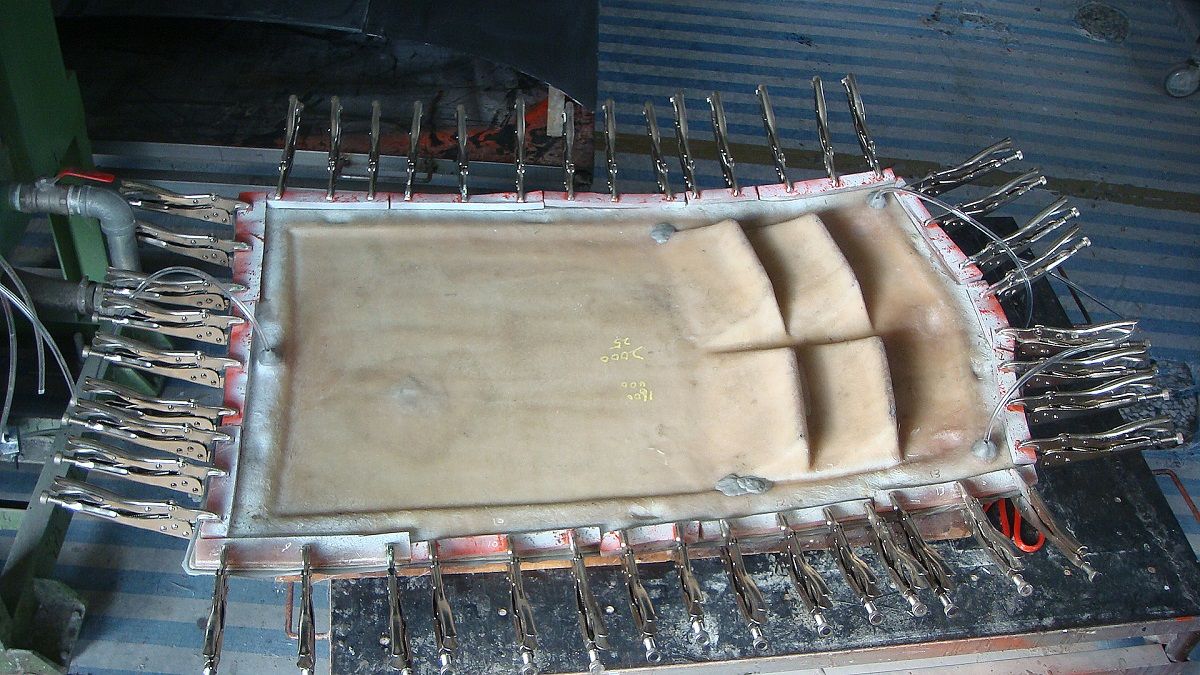
「真空抽吸加壓」是兼具品質與成本的最佳製造方式,製造時需要「內外模具」,先在外模上鋪設碳纖維布,之後套入內模,其上有管子用來抽吸內外模間的空氣,內模將會緊緊壓住碳纖維材質與外模,另一條管子可讓環氧樹脂吸入模具中。
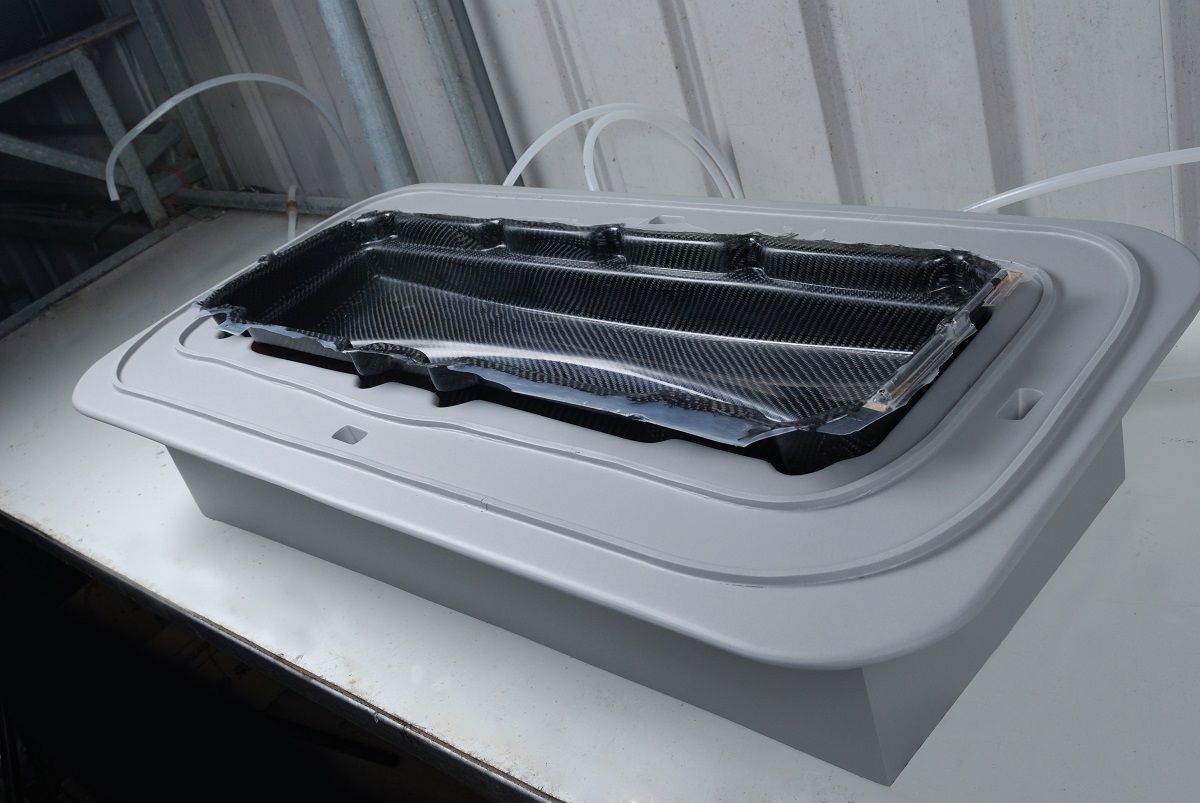

真空抽吸加壓製成的產品,不只內外層表面都看得得碳纖維紋路,厚度也超薄重量更輕,成品厚度約1.5mm(手積層碳纖維件厚度約6mm),重點是產品精度高、耐熱性也佳,是高檔碳纖製程。
而此製程有何優點?完成後的產品不只內外層表面都看得得碳纖維紋路,厚度也超薄重量更輕,成品厚度約1.5mm(手積層碳纖維件厚度約6mm) ,重點是產品精度高,因此即使製成集氣箱,也不用擔心上下蓋子會裝不上去,或對不到螺絲孔等問題,能在節省製造成本下,又不會犧牲產品品質,是目前國內外各廠商極力發展的碳纖維部品製造技術。
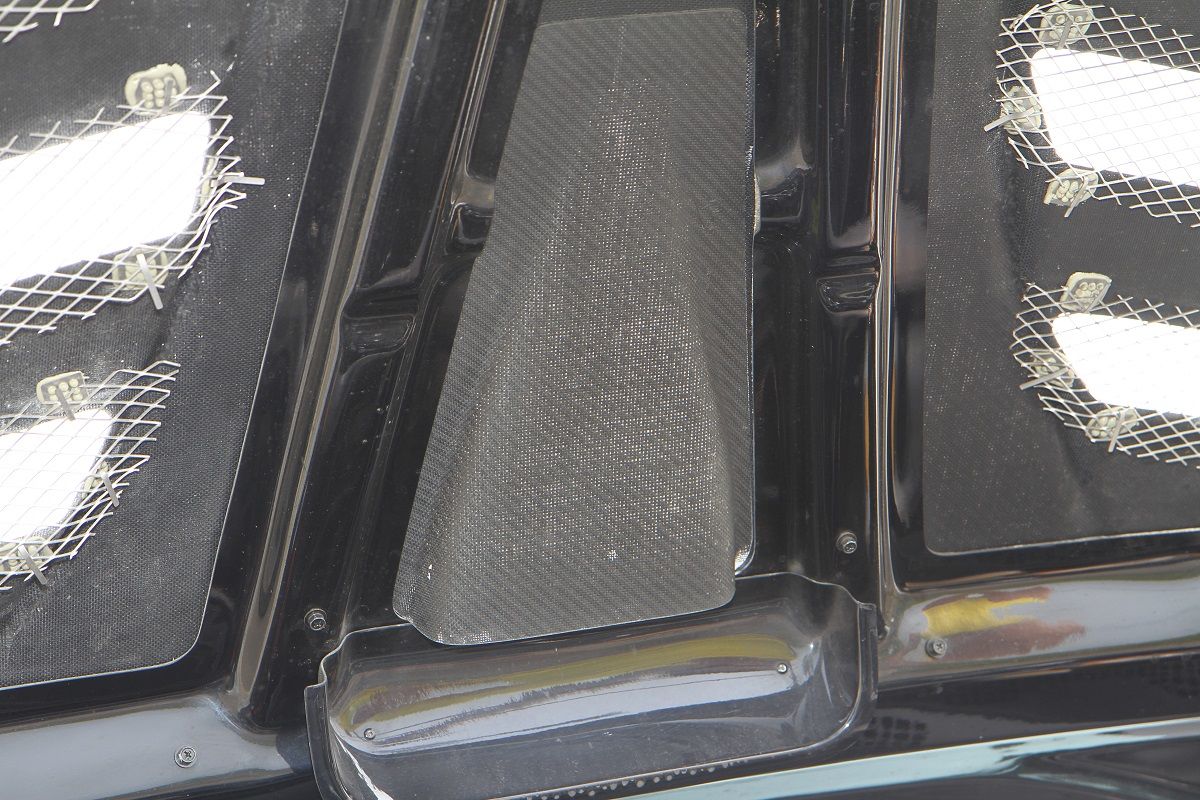
此為採用真空抽吸製作而成的碳纖維引擎蓋,可以從背面紋路看出是真正的碳纖維製品,而非以FRP為底的半碳纖維製品,重量輕且強度不會因高溫而軟化。
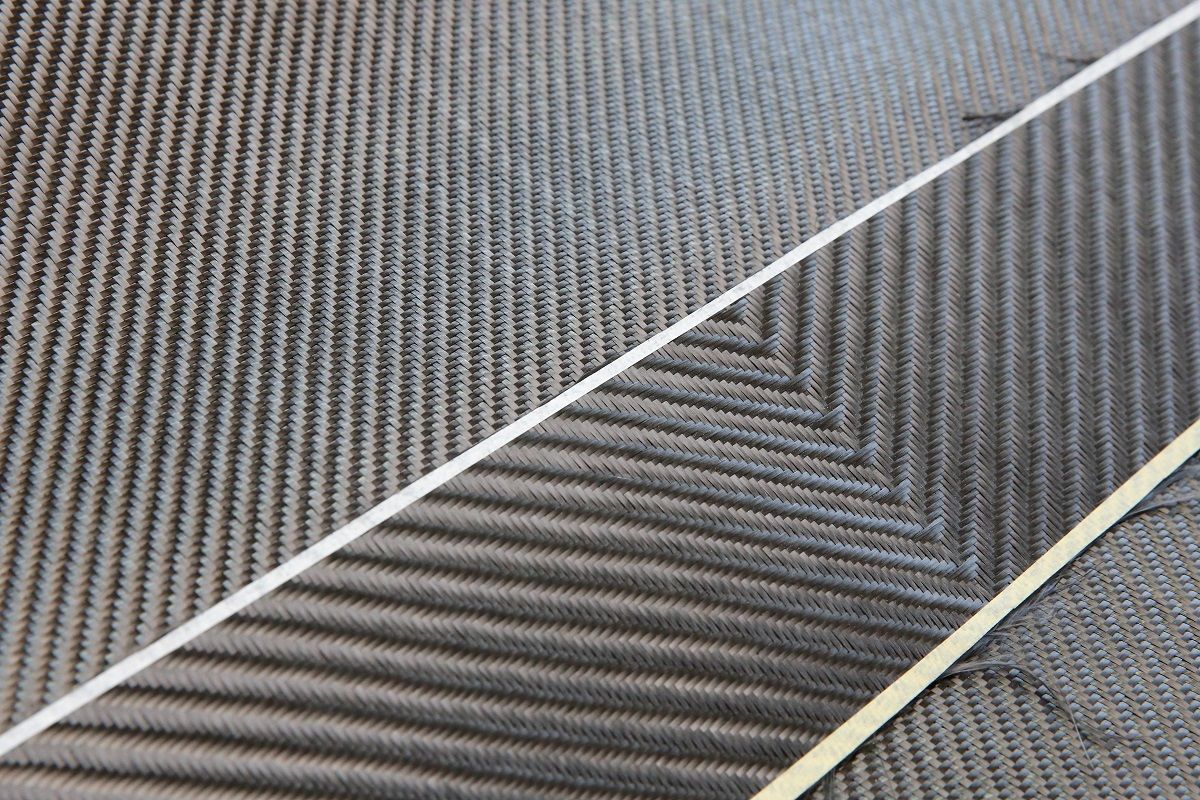
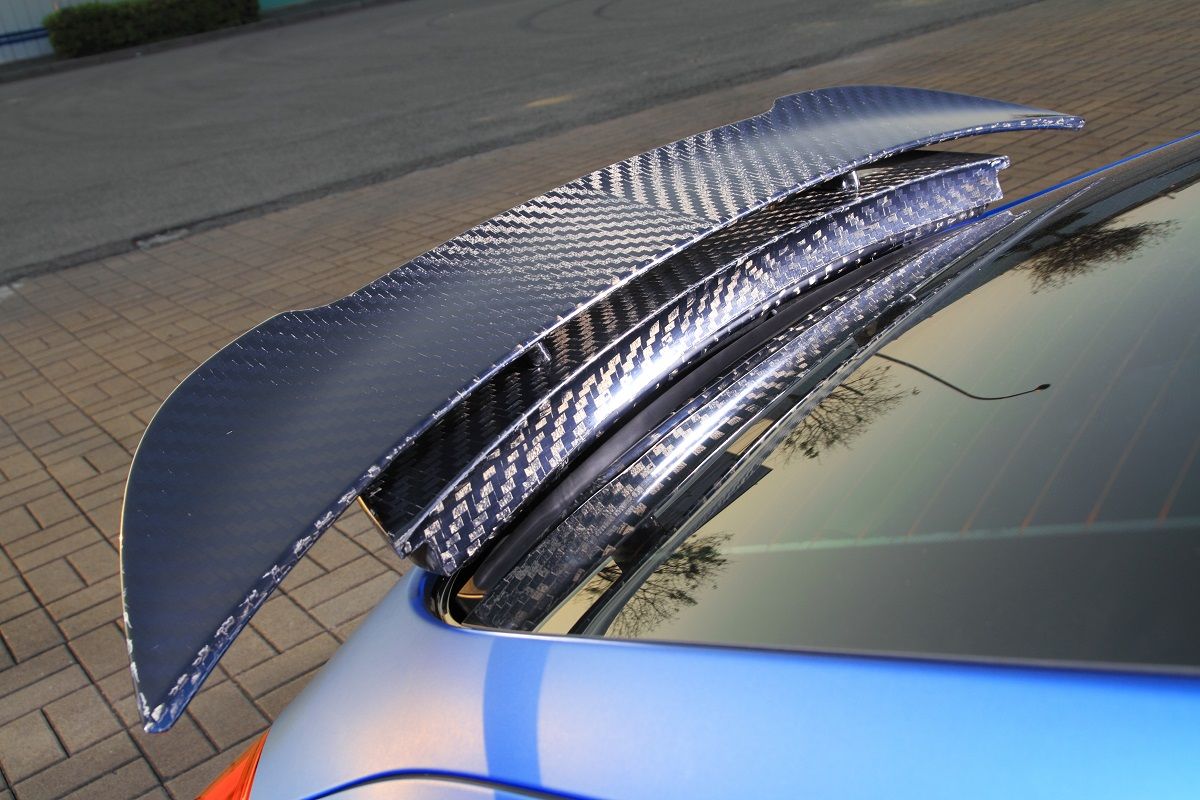
碳纖維紋路還可以K數來區分,K數是指一束碳纖維中有幾千根的單絲,3K就是指一束碳纖維中有3000根單絲碳纖維,12K就是指一束碳纖維中有12000根單絲碳纖維,反映在紋路上就是K數愈大紋路愈大塊。
問題八:有些碳纖維部品可以做到很薄,例如安裝在車內的碳纖維飾板,這是什麼種的碳纖維製程?
最費工的製程技術-熱壓成型工法
問題中所提到的碳纖維引擎蓋,應該是以熱壓成型製造而成的部品,「熱壓成型」製程有別於前述的手積層技術,且就連使用的原料也不盡相同。手積層所使用的碳纖維布就是一般布料,可摸到纖維絲、觸感軟趴趴,但熱壓成型可就不同了,其所使用的碳纖維布已經加入「Epoxy」(環氧樹脂),可使碳纖維布變硬、且附有彈性,而且摸起來會黏黏的,平常需要冷藏保存,也因為經過加工,所以光是原料就比手工披覆所使用的碳纖維布要高出2~3倍左右。
由於製造過程中需透過高溫+高壓來成型,因此必須使用鋼製模具,所以在產品製造前需要精準丈量尺寸,才能製作模具,而且需要正反模具才能成型,故需要「一對」鋼模來製造,不像手積層只需要一個。而熱壓成型的過程其實不難了解,成型過程中需加熱到130~140℃左右,同時也會加壓使其成型,因此製造過程需要專用的熱壓設備,產品越大所需要的熱壓設備也越大,成本當然相對提高,這些種種原因都是熱壓產品無法在汽車市場上普及的原因。



此為「熱壓成型」工法會使用到的鋼製模具與熱壓機,由於製造過程需要專用的熱壓設備,產品越大所需要的熱壓設備也越大,成本當然相對提高,這些種種原因都是熱壓產品無法在汽車市場上普及的原因。
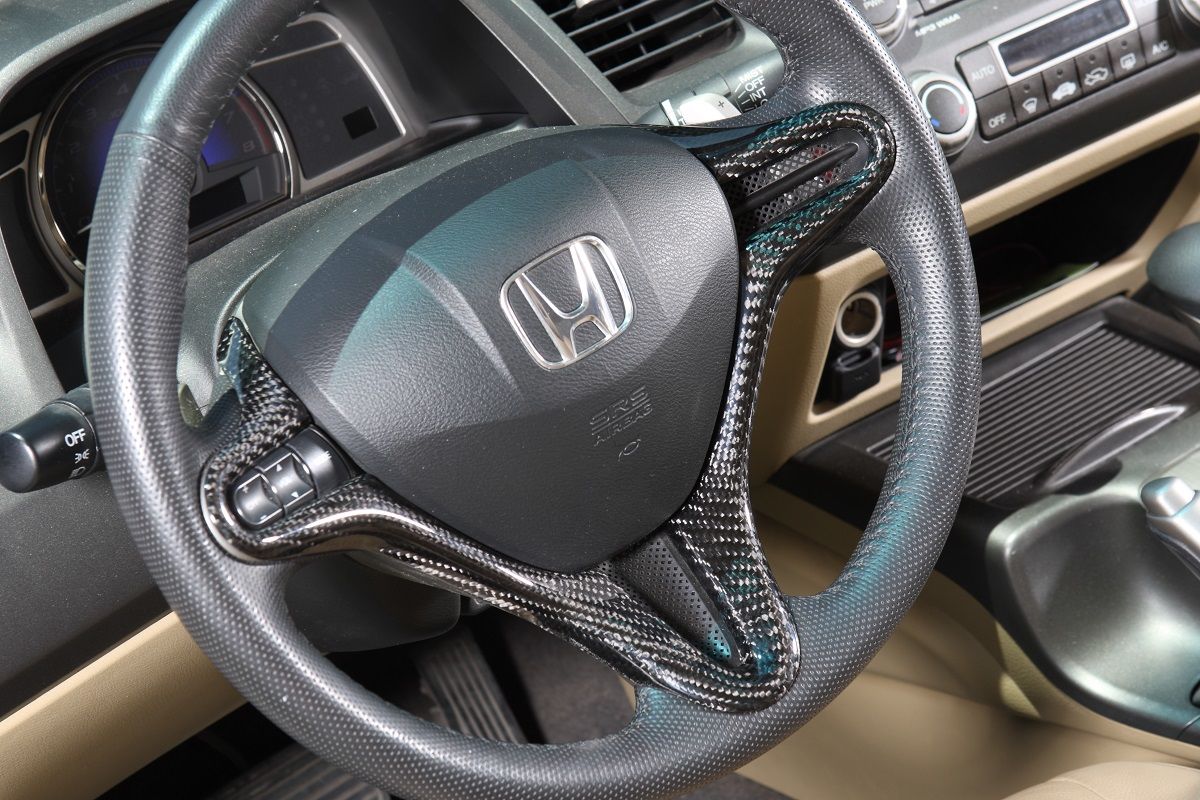
傳統手積層披覆碳纖維無法使產品細節突出,體積過小的產品也有製作困難度,使用熱壓成型工法反而可以解決這些問題,因此愈來愈多的汽車用碳纖維後視鏡、方向盤、中控台與排檔座飾板等,都可見到熱壓成型的「薄型」碳纖維部品。
不過隨著碳纖維產品需求量大增,運用性也越來越廣,汽車用熱壓產品也有逐漸增加的趨勢。正因為傳統手積層披覆碳纖維,無法使產品細節突出,體積過小的產品也有製作困難度,使用熱壓成型反而可以解決這些問題。汽車的後視鏡、晴雨窗、方向盤、中控台與排檔座等碳纖維部品,都可以善用熱壓方式來製造,畢竟這類飾板的面積小,所需要的模具、熱壓設備也會相對縮小,可以更有效控制成本,再者、熱壓成型的產品厚度薄如紙,運用於飾板上恰到好處,可以有效提昇安裝後的密合度,是碳纖維內裝部品很常運用的製造工法。
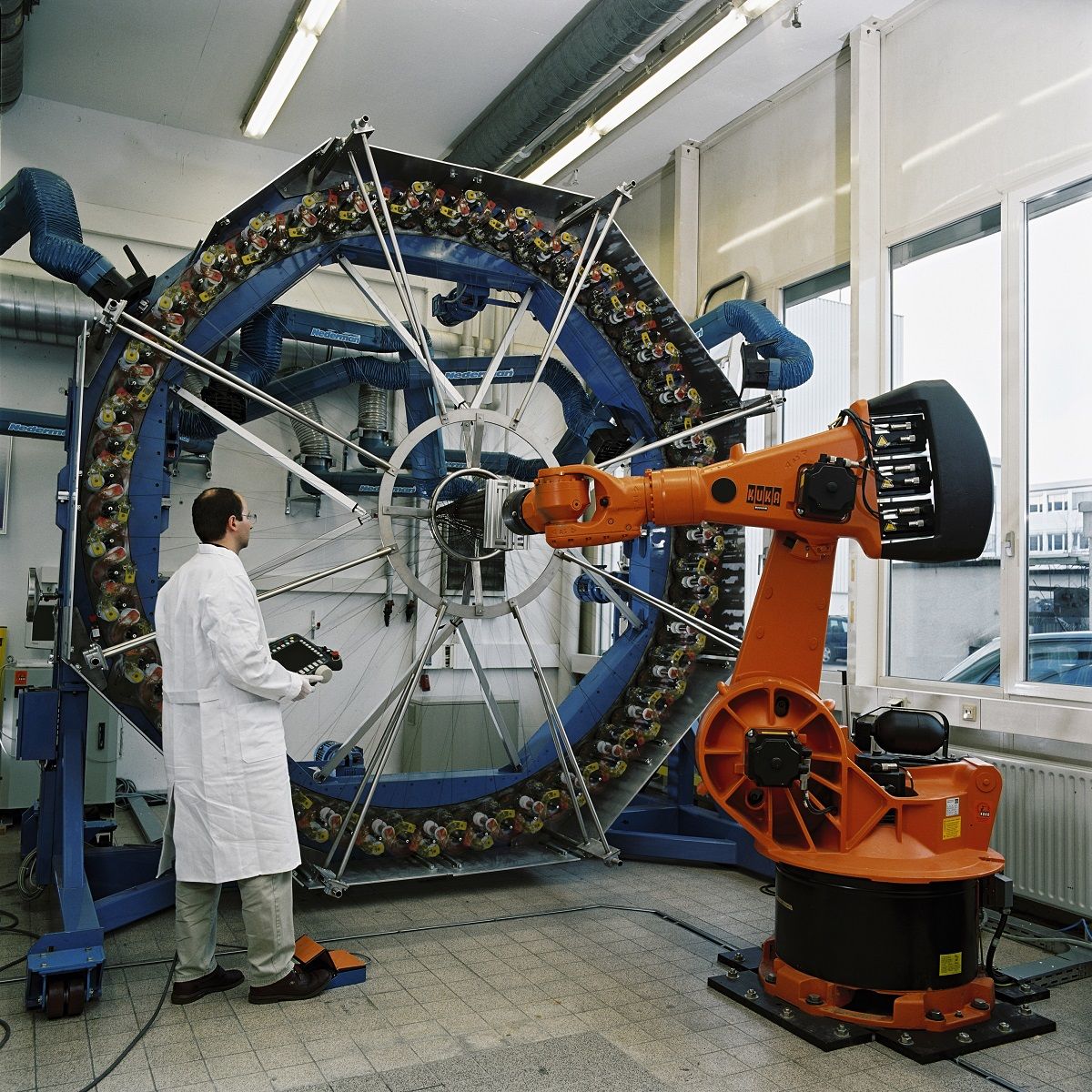
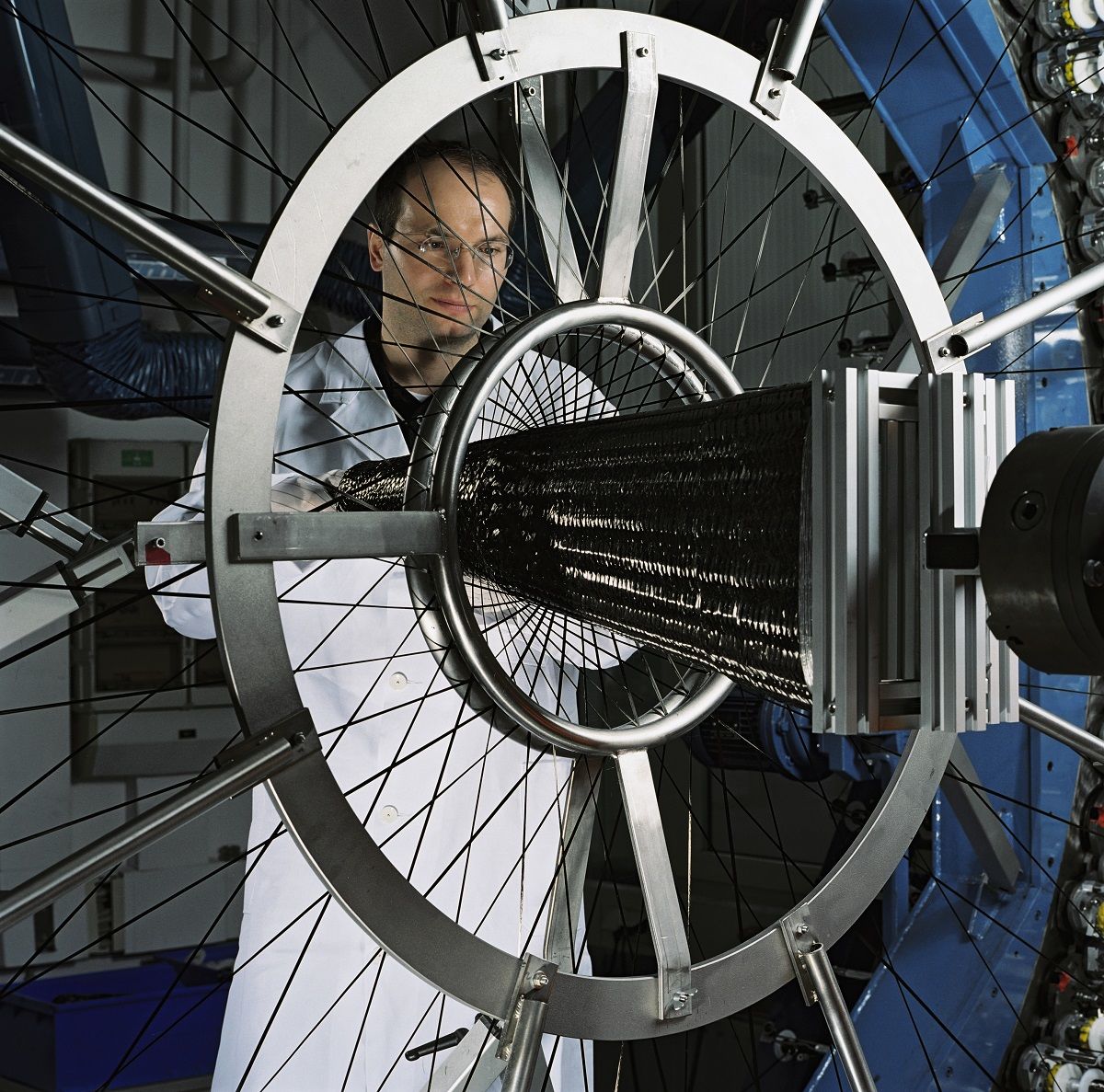
圖中為少數有能力打造F1賽車車架的公司才擁有的碳纖維部品生產設備,可以見到真正的碳纖維部品是透過碳纖維絲線一層層編織而成,
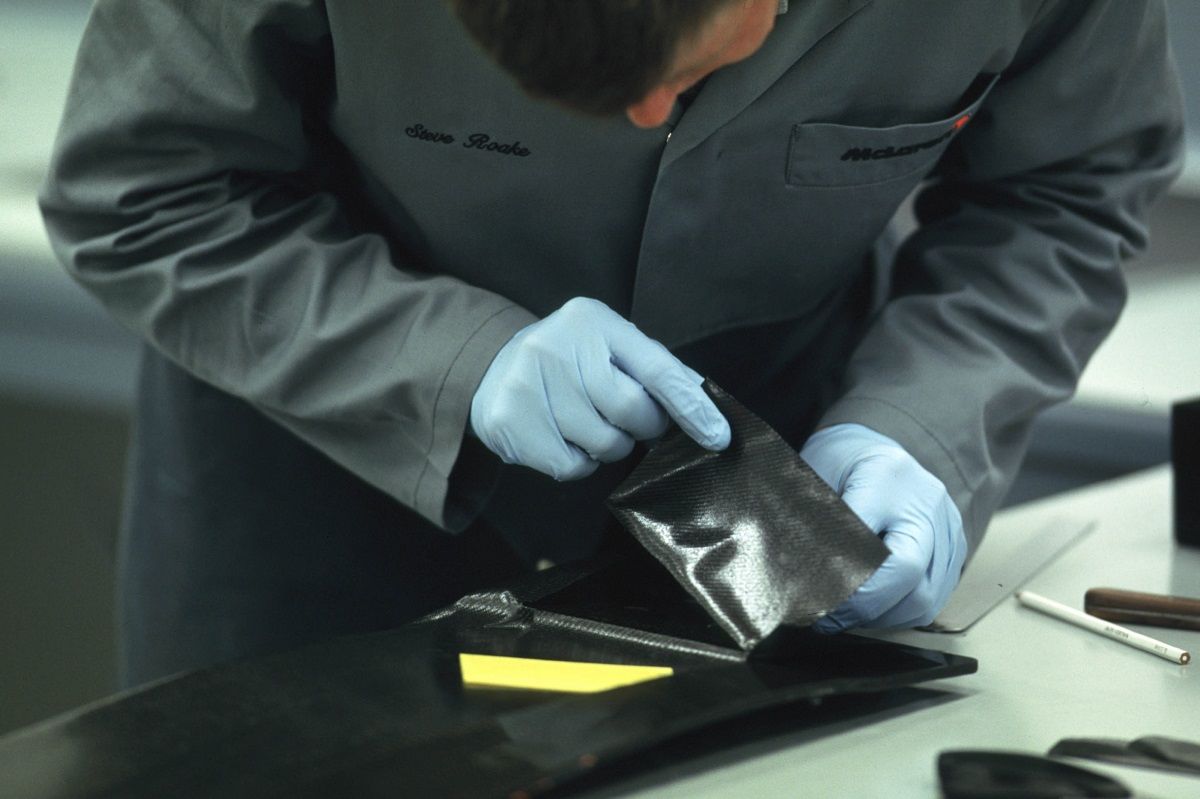
頂尖超跑上的碳纖維部品,也是利用碳纖維布一片片重疊起來,並且須經過高壓、高溫的真空爐的固形,來賦予碳纖維部品極強的剛性。