文 陳冠勳 / 圖 王澤瑋
原以為大喊一聲「芝麻開門」就能如入無人之境,大搖大擺的直闖輪胎廠,但實際上可沒那麼簡單。費了九牛二虎之力,徵詢多家廠商之後,咱們終於獲得建大輪胎的善意回應。頂著南台灣的烈日,換上工作服,我期待以久的黑輪日記即將開始。不過,別說我沒提醒你:「怕熱就別進來!」話說輪胎的結構,表面上雖看似簡單,但事實上,要成為最終的「橡膠彈性體」,它的製造程序可不能像放入我們口中的巧克力甜甜圈一樣,用三言兩語就可以輕鬆帶過。尤其這顆內含百種以上的黑輪混合物,除了要有彈性,對抗來自四面八方的慣性拉扯,還得兼具行駛中最重要的抓地力,其背後的製程想必一點也馬虎不得。廢言不多說,輪胎生產線的辛苦與趣事在哪,讓我一次說個明白。
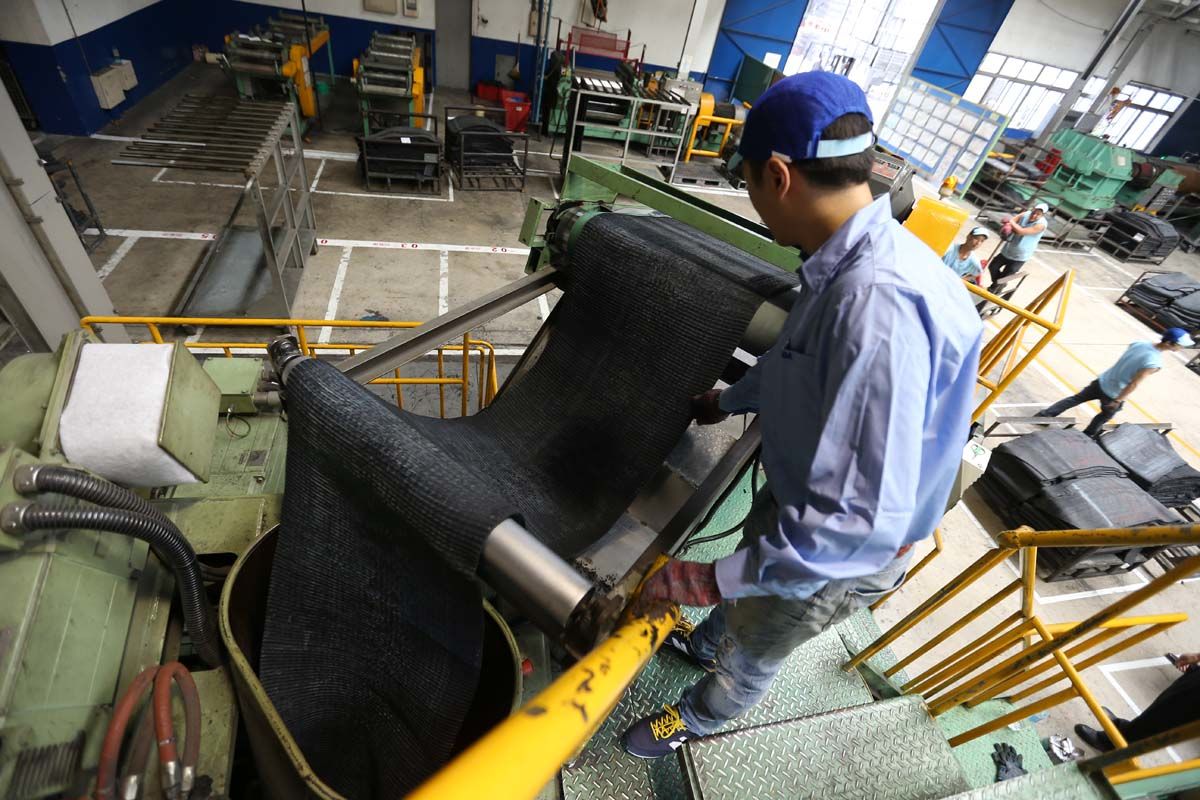 |
要製造成胎面膠的膠料經過流道後將進行一連串的預熱,塑型與組合。 神秘的混煉 難窺真實 講到輪胎的製成,大致上製成可區分為「混煉、備料、成型、硫化、檢驗」五大階段。其中最重要的就是第一階段的原料「混煉」步驟,屬各家輪胎廠中最為關鍵,也最為機密。在這個階段中,混合了諸如橡膠、硫磺、碳煙、抗氧化物……以及多種添加劑,並按比例透過密閉式的混煉機加以均勻地混煉而成。當然,為符合市場的需求,以及輪胎的使用特性,工廠會針對輪胎每一種膠面所使用的膠料進行成分調配,而這也就成為了輪胎最終能表現其性能的關鍵要素之一。講了那麼多,到底還是礙於商業考量的因素,關於混煉的工序、內容物和比例為何,我們只能限於概略的文字敘述,而無法參與實際的操作。但從混煉機所產出的「橡膠半成品」,進入在下一階段的「備料工程」中會有什麼樣的加工過程,先補充好水分準備上工囉! |
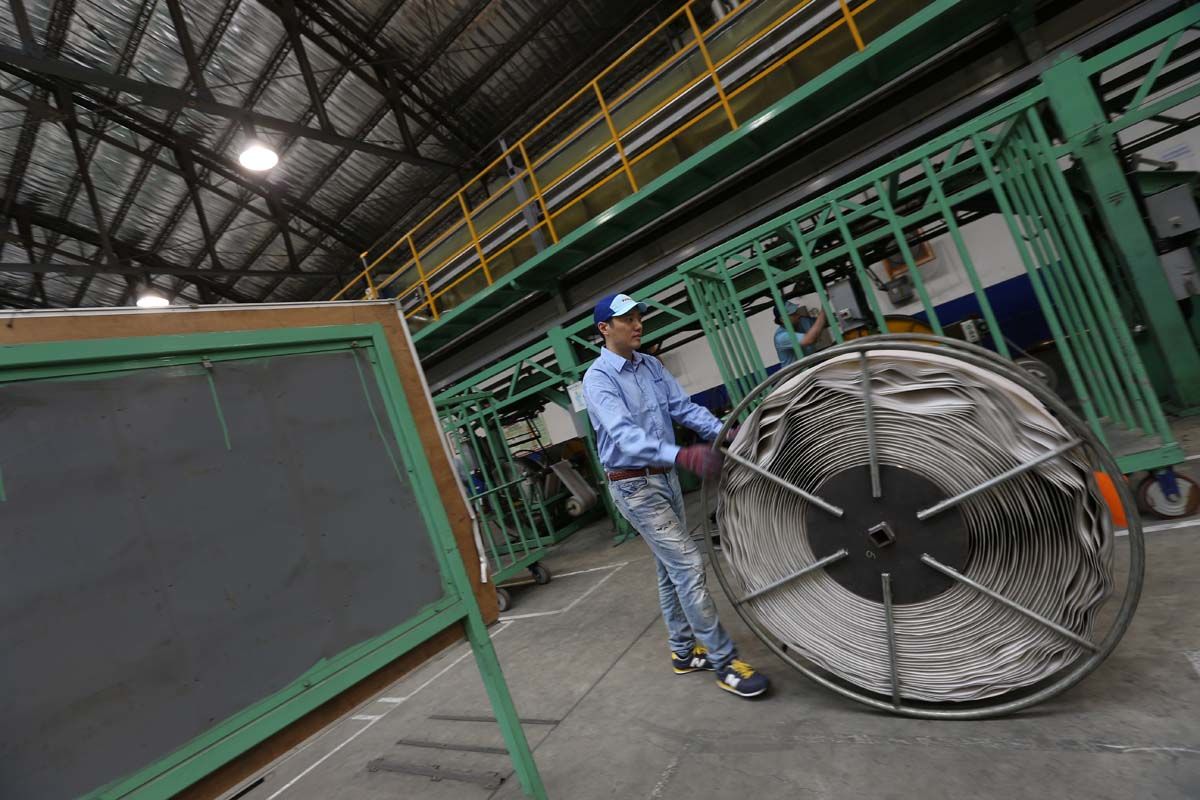 |
利用收容布來捲收這些的半成品有利於運送到下一階段進行加工。 要用擠的 前往「備料」廠房之前,廠區主管或許是擔心我這隻待在冷氣房工作的飼料雞,禁不起工廠的悶熱,再三好意的提醒:「裡頭可是很熱的!你要有心理準備。」其實,走進偌大的廠房內,看到眼前一條條正在運轉中的輸送帶,對迫不急待想了解箇中道理的我來說,早已把剛才的叮嚀拋到腦後。在備料工程這個階段中,「擠出」將會是一個很重要的動作,它所擠出的半成品膠部件包含了胎面膠、胎邊(側)膠和具有補強功能的三角膠,而它的原料來源,其實就是先前透過混煉機所製成並切割成特定長條狀的橡膠半成品。這時候,我的任務就只要緊盯著台車上的原料是否安然地進入機器中,並讓原料能夠不斷地接續下去。只不過當我實際抓起看似軟趴趴、輕綿綿的橡膠半成品準備送上輸送帶時,頓時橡膠扎實的重量讓我一度笨拙得不知如何施力。 |
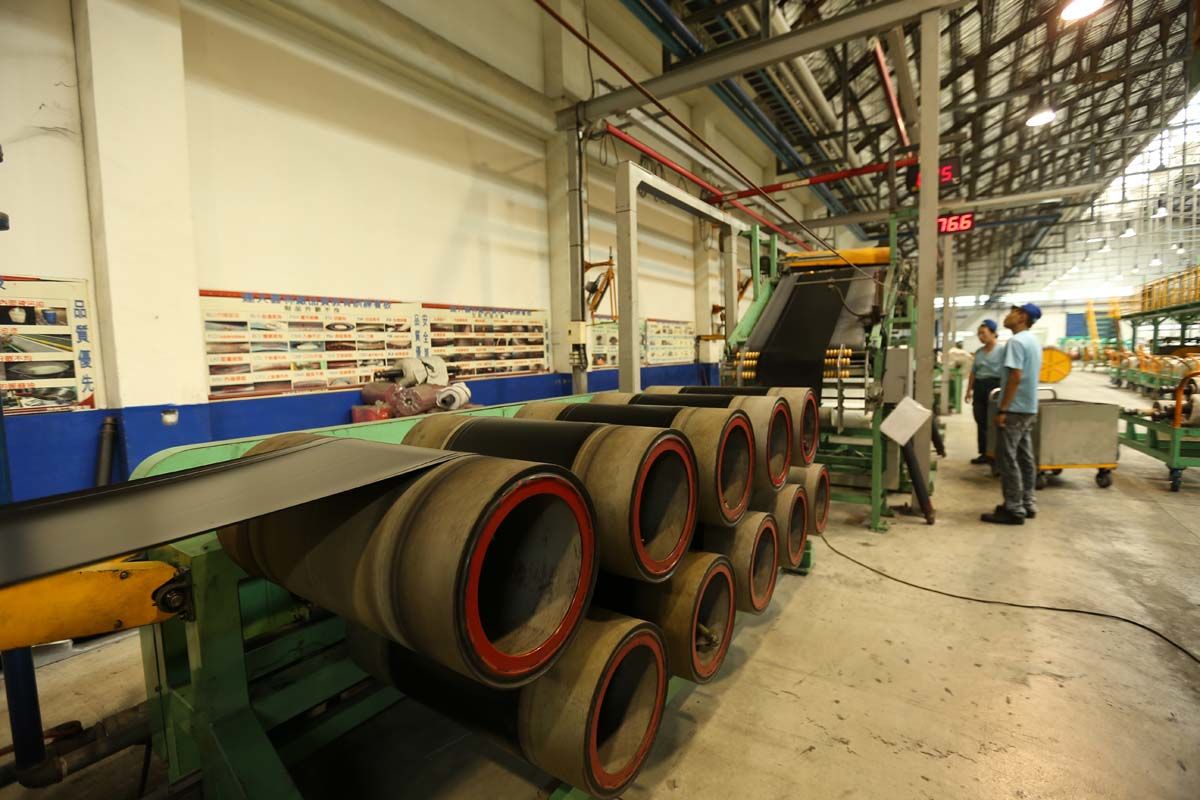 |
製造輪胎底層的內面膠會利用壓延機壓出輪胎內面所需的寬度和厚度。 一邊實作,一邊好奇的問著廠長,「這些黑黑的『麥芽膏』等一下會往哪走?」他說,這條生產線最終將會產出輪胎最外層的「胎面膠」。換言之,在擠出成型之前會將三種不同成分的膠,經由各自的輸送帶與流道,開始進行預熱,塑型,最後則是將三者組合,融為一體,並經過設計好的口徑擠壓出來,成為產品所需要的形狀和尺寸。當然,考量到方便運送到下一個階段,此時會以「收容布」來捲收這些產出的半成品。但要小心的是,捲收半成品的鐵輪可是沒長眼,所以廠區規定每個人作業人員得穿鋼頭鞋,也是為了避免作業時的意外,否則,一不小心腳趾肯定會成了肉醬。 |
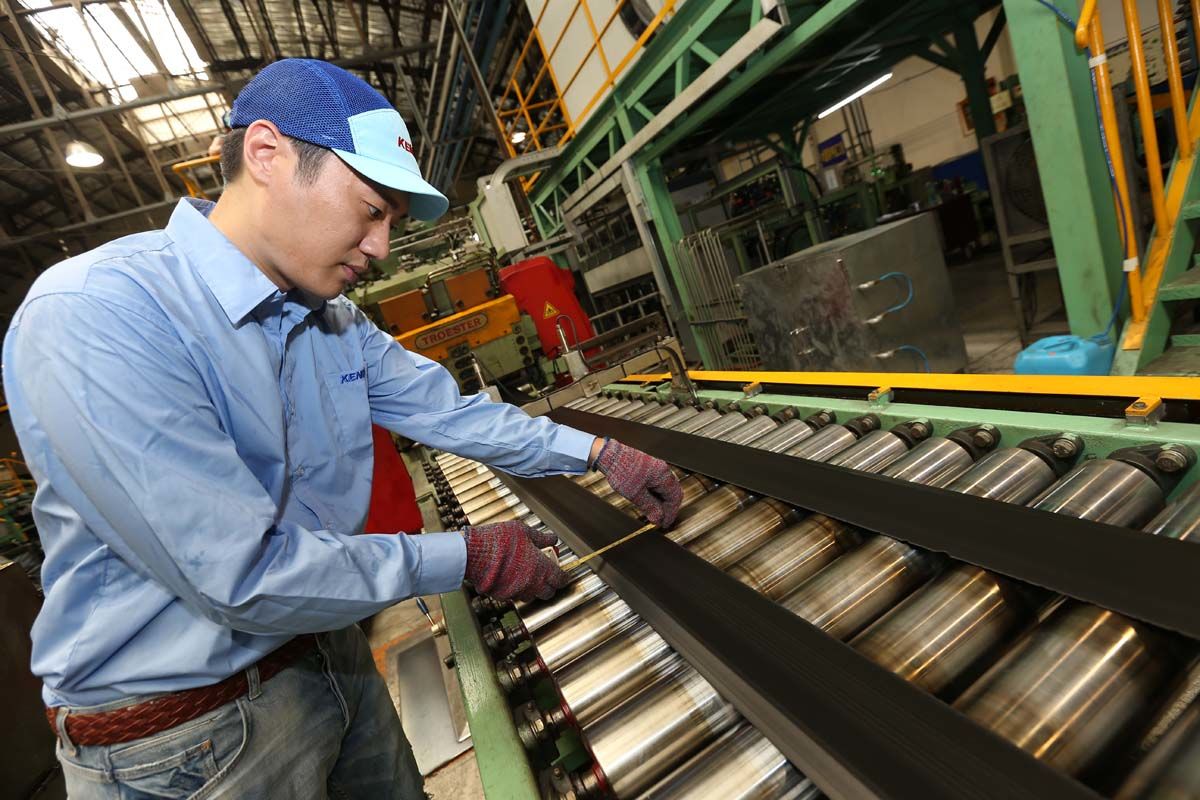 |
檢查由壓延機壓製出來的胎邊(側)膠寬度是否符合規定。 壓完之後開始裁 由於輪胎是層層堆疊而成的,裡頭的原料更不乏膠料與其他材質。比方說原本為了取代傳統輪胎內部的內胎,以及防止輪胎氣體外洩,達到完全密封,不透氣的狀態,此時構成無內胎輪胎(Tubeless)底部的「氣密層」就顯得十分的重要。當然,構成氣密性佳的膠層所需的特殊材料則被稱之為內面膠(或稱內襯膠)。製造的方式,是將內面膠利用壓延機來壓製出輪胎內面所需的寬度、厚度,但由於內面膠具有高黏性,所以在進入下一個階段加工之前,同樣在收容的時候得在層與層之間加上襯布隔離。 |
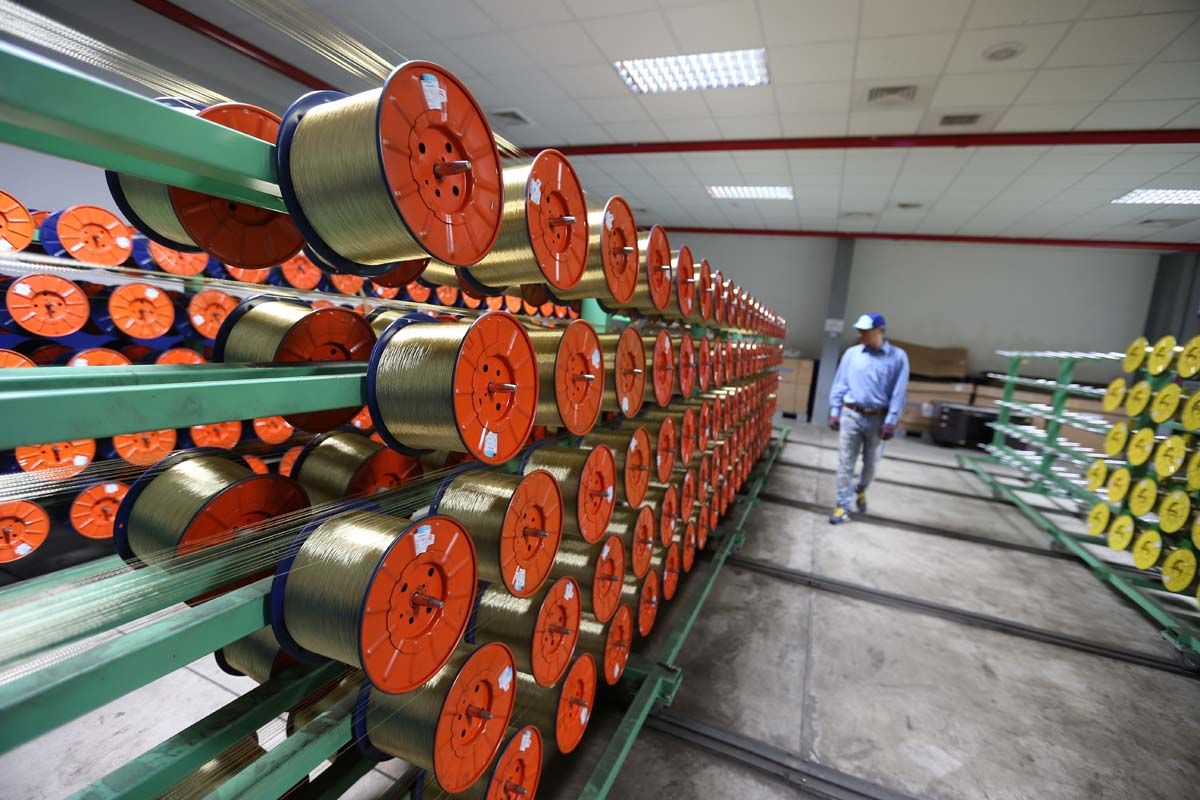 |
需一一檢查架上的每一綑鋼絲是否有脫落的情形。 另外,位於輪胎氣密層的上頭,則會再鋪上由強韌纖維製成的簾子布和鋼絲材質,而這兩者是輪胎製造過程中不可缺少的元素。當然,以上兩種材料在可以成為對胎體箍緊,使胎體具備高張力的特性,並足以支撐輪胎荷重,以及抵抗遭異物穿刺的保護層之前,得先經由壓延機將膠料各自與這兩種材質進行壓延包裹。最終,便能成為所謂的「簾布覆蓋層」和「鋼絲環帶層」了。接下來,當簾布的兩面與較薄的膠料緊密結合後,成為簾子布覆蓋層時,將進入所謂的「簾布裁斷工程」。此裁斷機作業的用意,是為了因應輪胎的尺寸、大小的不同,裁切出適合輪胎所需的長度和角度。所以,在稍後「一次成型」時,簾布層將與「內面膠」、「胎邊」、「三角膠」和「胎圈鋼絲」做結合。值得一提的是,一走入製作鋼絲環帶層的廠區時,最明顯的感受就是「舒服」。這樣的直率並不是說裡頭有專人在侍候著,而是該區為了避免鋼絲生鏽,得全年維持著恆溫恆濕;所以廠長說,尤其是夏季,這裡比起廠區其他濕熱難耐的地方,更顯得舒適宜人。 |
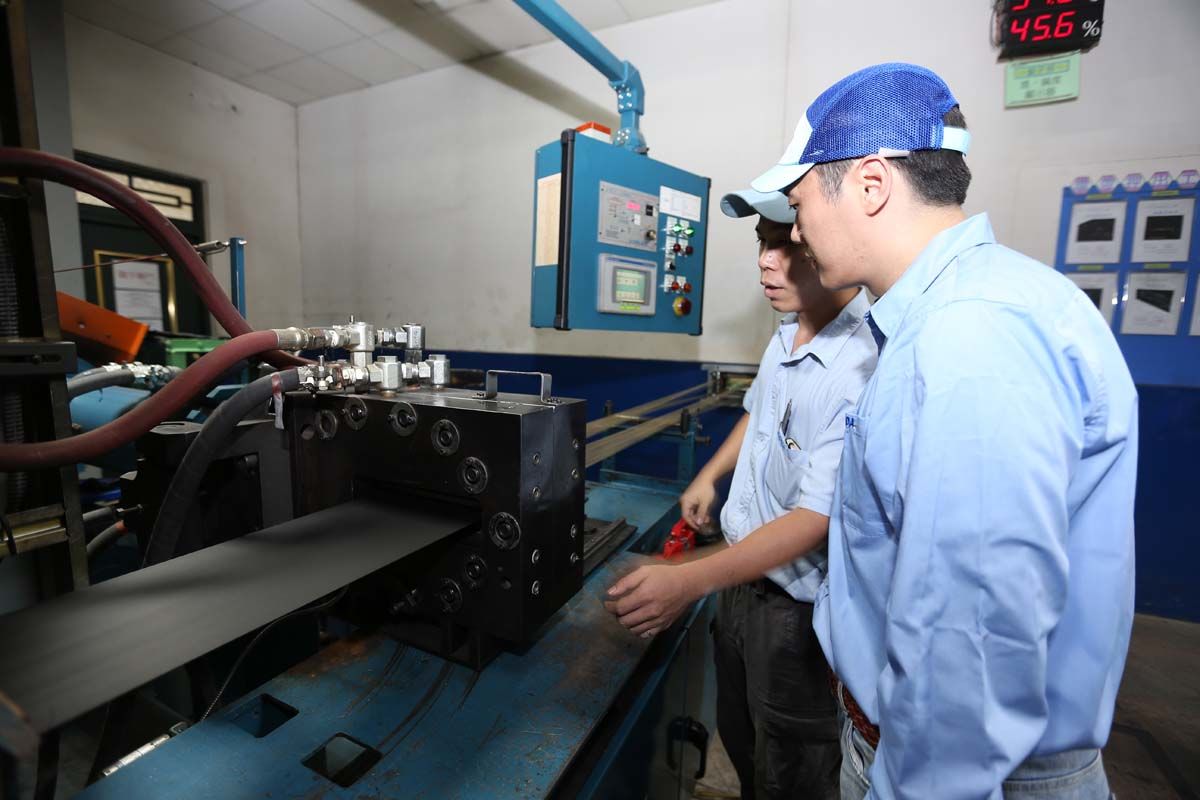 |
當鋼絲與膠料的結合便形成了保護輪胎的鋼絲環帶層,但為了避免鏽蝕的情形,在這個區域中必須讓溼度保持在50%以下,溫度約27度。 |
輪胎的穩定與安全就靠它了
為了使輪胎與輪圈能夠緊密的結合,以及在駕駛的過程中保有一定的操控性與安全性,「胎圈鋼絲」便扮演了十分重要的角色。簡單來說,胎圈是由「胎圈鋼絲」和補強胎邊的「三角膠」所構成的。胎圈所指的範圍是,輪胎內緣與輪圈接觸的部分。但為確保輪胎與輪圈的密合度,之後還得加上按指定的圈數和大小所製作出的高強度鋼絲圈,最後,利用擠出機將鋼絲圈與三角膠(又稱胎圈填充膠)進行貼合。其實,三角膠是用來減緩胎圈的衝擊,並避免成型時空氣流入,以及最重要的「加強胎邊剛性」。因此,它所用的膠料硬度是輪胎中最硬的,而且當經過輪胎成型的最一個階段「硫化」後,這種特殊的膠料更能夠與鋼絲緊密的貼合。當然在實際機上操作「貼合」的過程雖不複雜,除了得手腳並用之外,更考驗著本身眼明手快的協調性。當然,比起一旁的大哥大姐那般出神入化的神速技法,我怎麼可能跟得上這種神領域般的速度;與其出錯連連,我還是乖乖地照著廠長的指示一步步小心翼翼的操作吧。
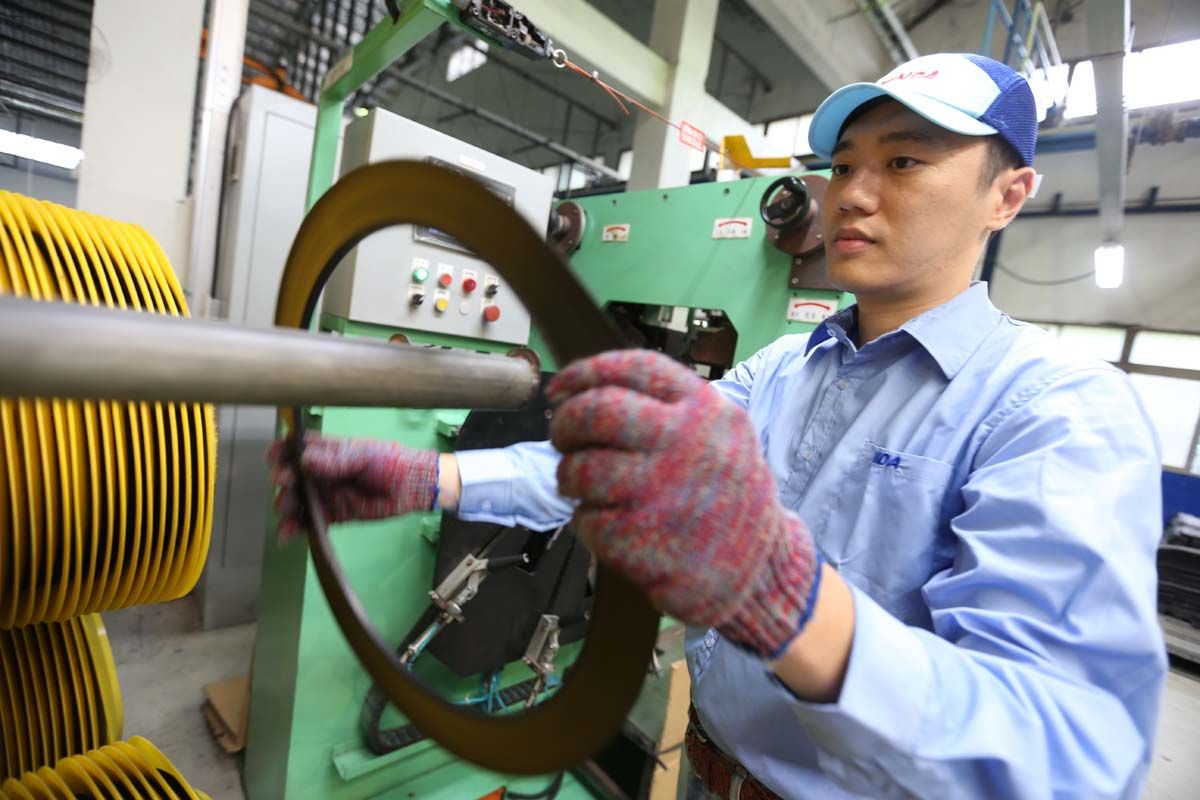 |
透過三角膠條貼合機將按指定的圈數和大小所製作出的鋼絲圈與三角膠進行貼合。 |
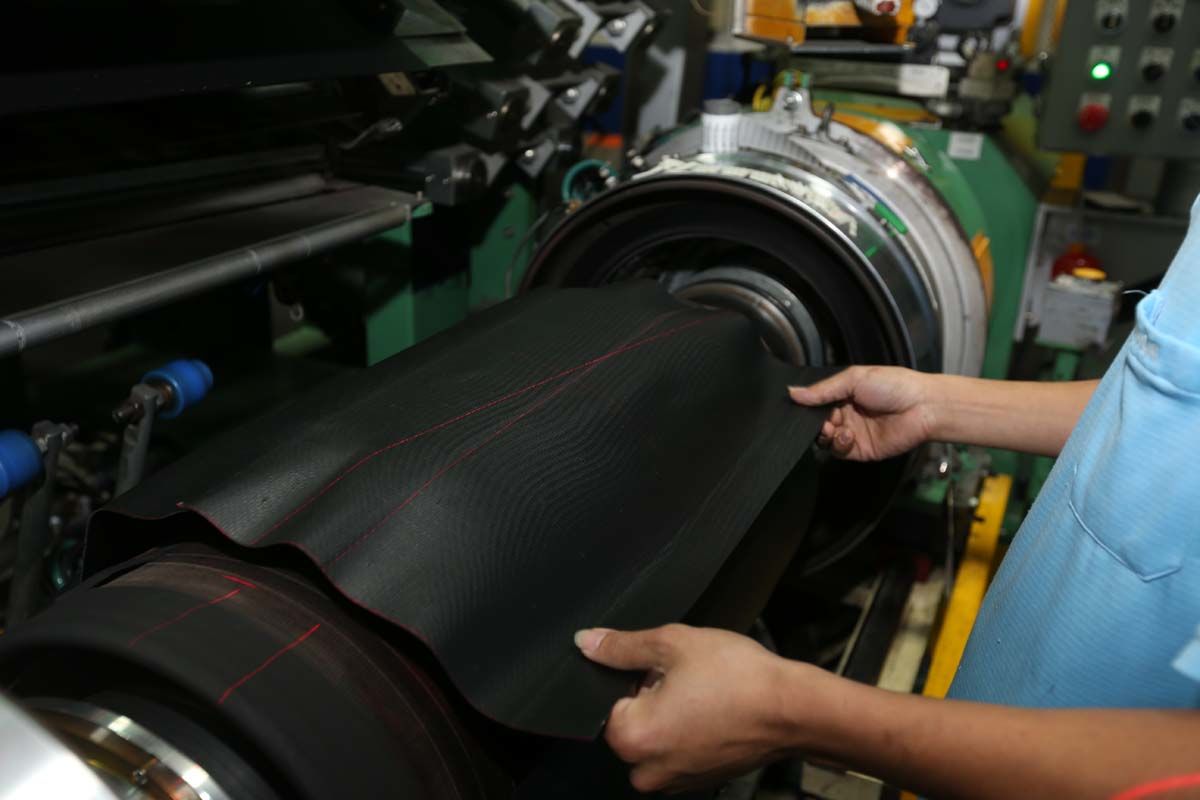 |
依據胎體成型筒上的設定線,將內面膠或簾布層拉出後,對正貼上。 |
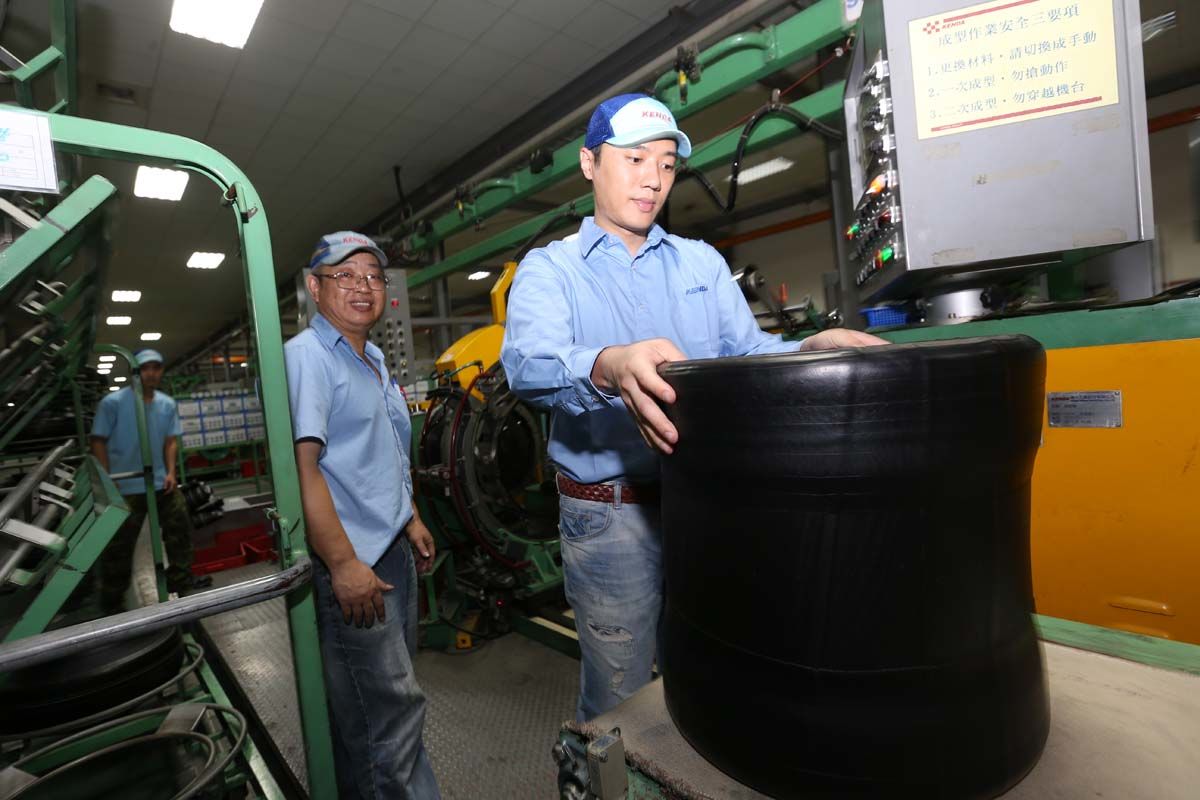 |
一次成型的半成品在兩側貼上胎圈後,形狀漸漸固定了。 疊疊樂 從生胎到定型 在第二階段的備料工程中產出的許多半成品,將在這裡一一被堆疊結合。事實上,輪胎的定型在這裡會分為兩個階段,第一階段是「生胎」,第二階段是「硫化」。簡單來說,生胎的製成是利用二次成型機,分為「一次成型」和「二段成型」來完成生胎的製作。在一次成型的階段,可說是反覆「貼布」的過程。因為在胎體成型筒上,操作員會將內面膠、簾布層、胎邊膠等等拉出、接上,並按照機器上頭的設定線加以對正。看著師傅操作幾輪之後,自己以為這不過是「簡單」的對準貼合罷了,於是躍躍欲試跑上去操作。只不過光是開始貼第一層的時候就讓我吃足了苦頭。不知是不是手拙的緣故,再加上橡膠本身的高黏性,一不小心,貼歪重來磨耗了我相當多的時間。好加在有師傅從旁指導和修正,讓我反覆操作幾次之後,自信心大增。 |
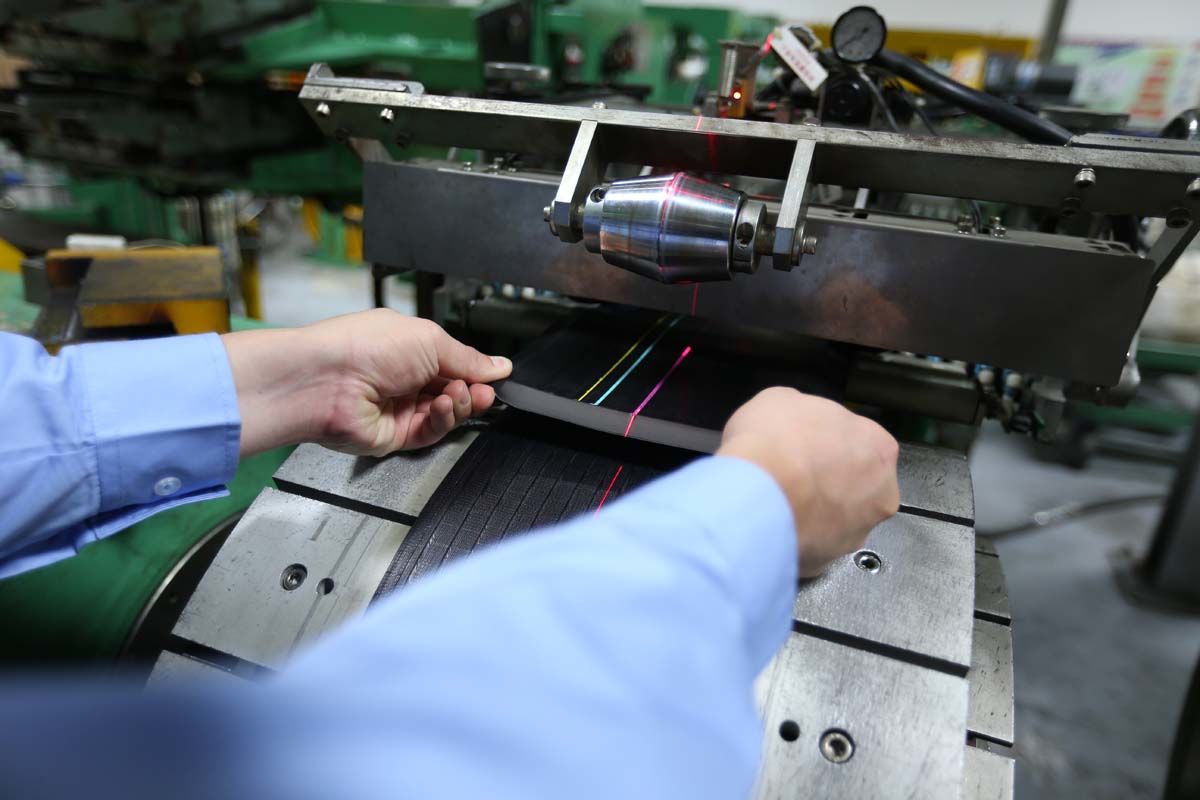 |
在束帶層成型筒上進行胎面膠的拉正貼合。 |
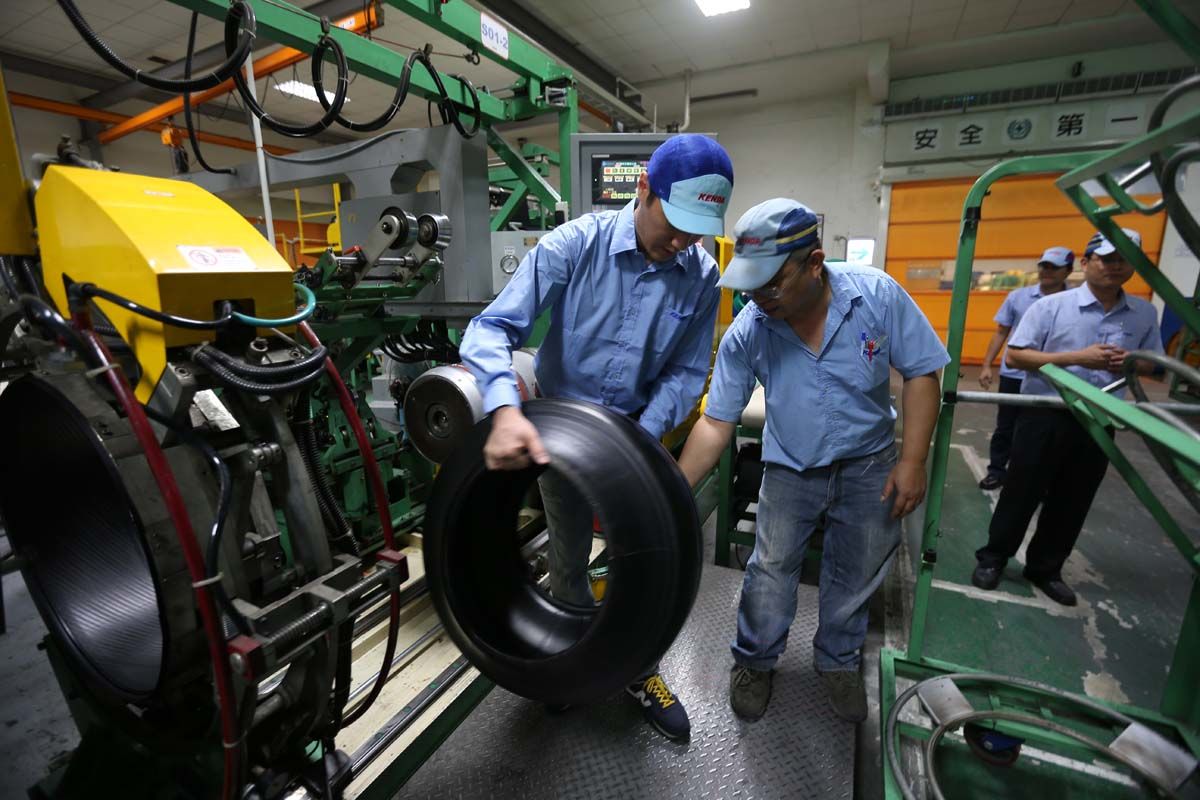 |
生胎完成加工後,檢查無誤就可以到下一個加硫的階段。 接下來,為了做成「生胎」,還得在機器兩側套上先前由三角膠和鋼絲圈結合的胎圈進行固定。第二個步驟,再將鋼絲環帶層、尼龍束帶、胎面膠等等在束帶層成型筒上進行貼合。最後,再利用機器向內充氣擠壓結合,此時二次成型的結果便完成「生胎」。取下沉甸甸的生胎,並依序堆放後方的層架,待由其他人員拉車到下個階段進行最後的加工「硫化」。 |
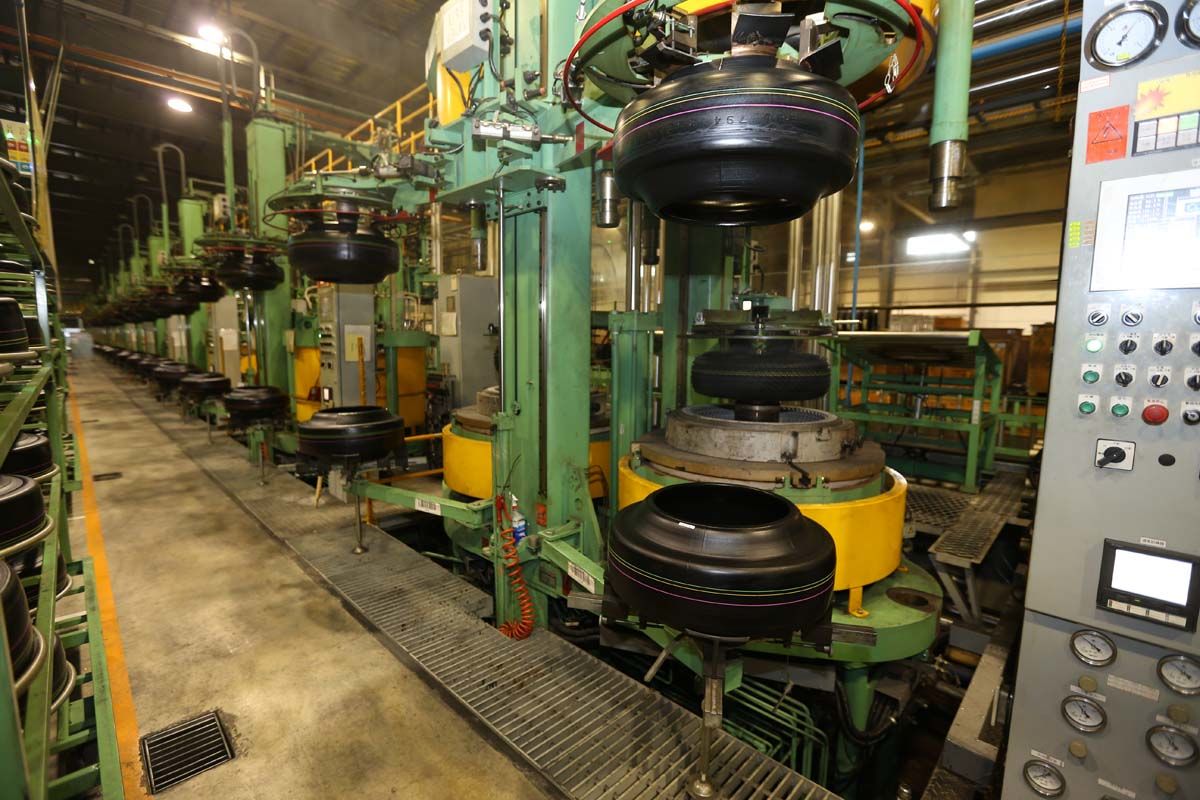 |
將生胎放入垂直加硫機,以高壓高溫讓橡膠與硫化產生化學反應,製造出最終的輪胎模樣。 |
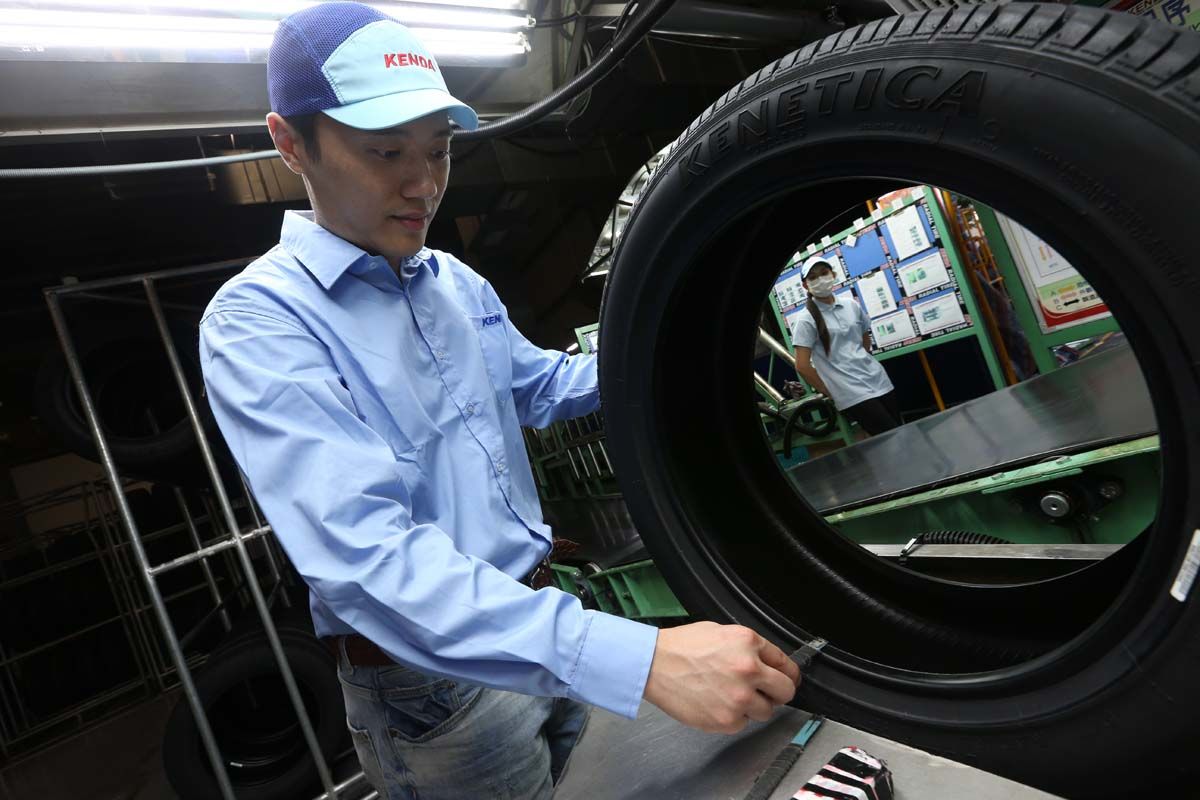 |
胎圈多餘的橡膠毛屑要仔細檢查並刮除。 有了輪胎的雛形後,生胎還得經過硫化加以定型。在進入垂直式加硫機之前,得靠人力搬運的方式,一一將生胎下鍋處理一番。利用高壓高溫讓橡膠和硫磺產生化學反應,使輪胎的強度、彈性、耐磨力、抗腐蝕等特性,發揮到最大。而且硫化機裡頭放置了具有花紋的模具,在約莫15分鐘後,胎面就會呈現模具上的花紋,連同胎邊的規格資訊也是在這個階段製作出來。 |
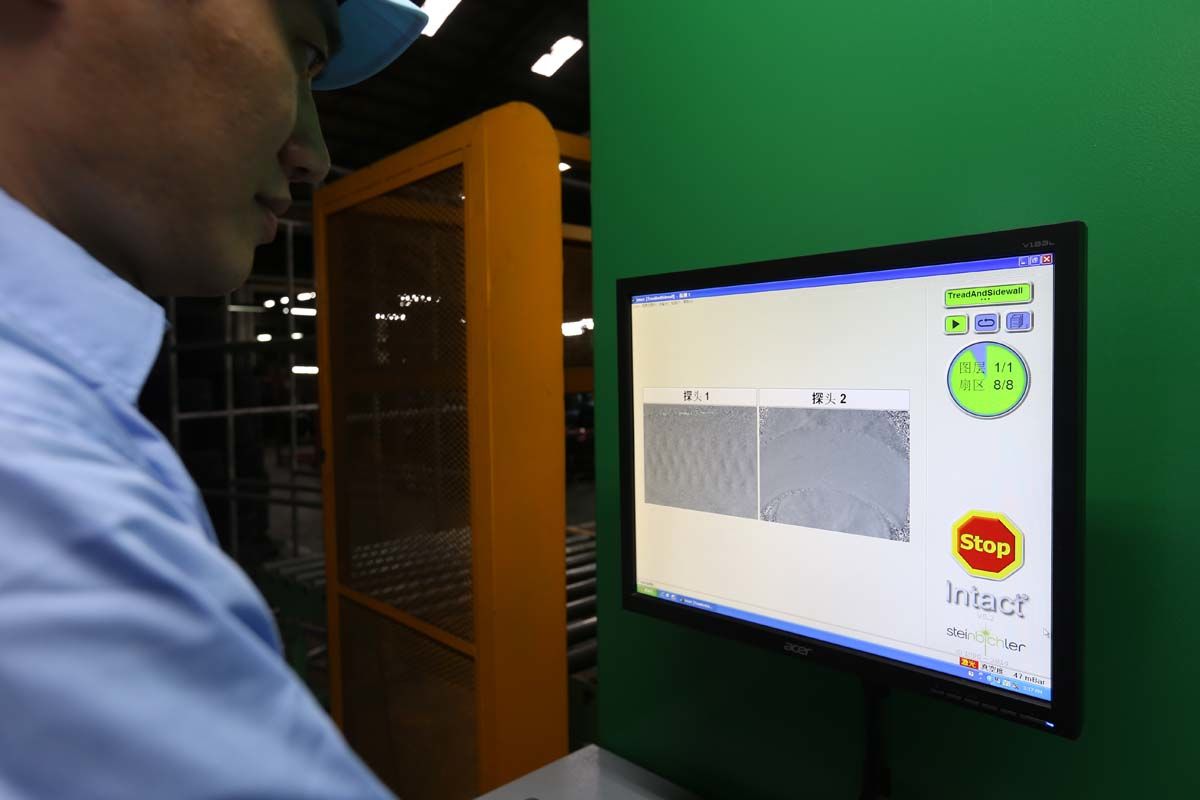 |
輪胎進入X光機,利用雙探頭將影像投射到螢幕檢查有無缺陷。 |
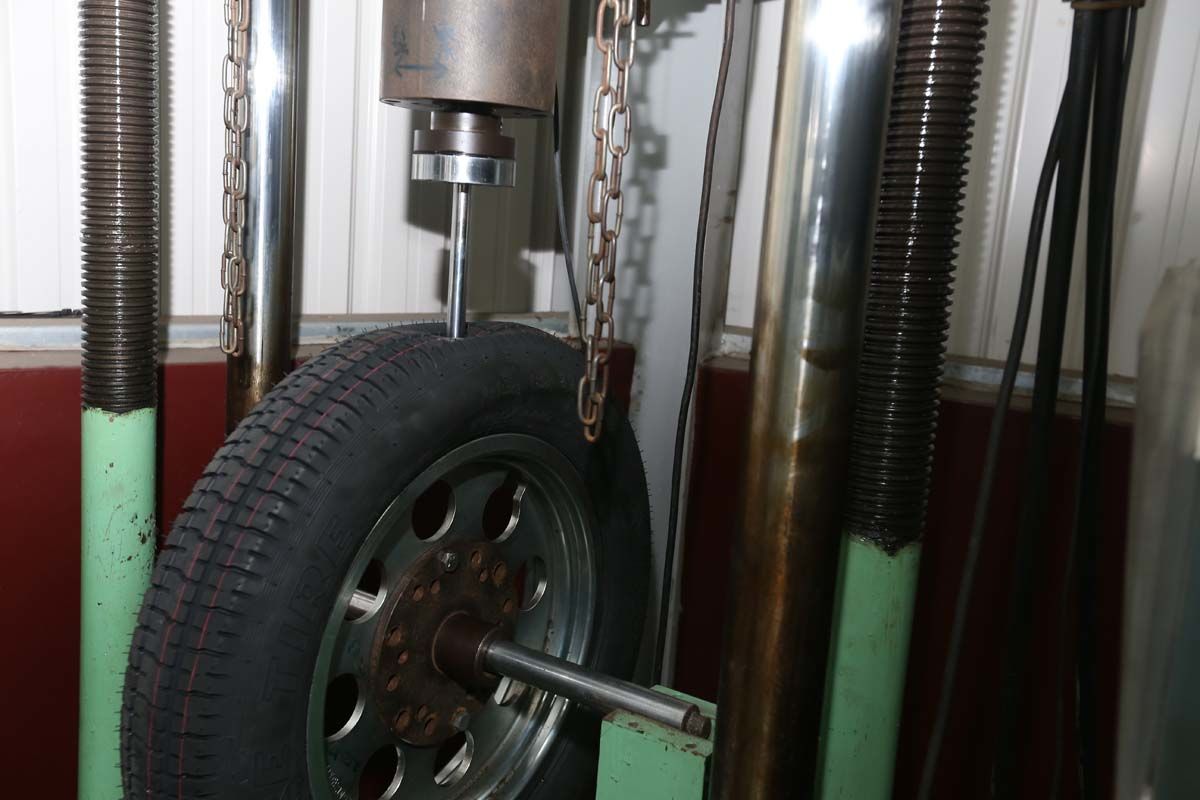 |
將輪胎置於破壞能測試機上,以垂直動能持續對胎面施壓。 修邊、檢驗,準備貼標出貨 胎製成的最後一道手續,就是「檢驗」。在外觀方面,因為加硫的過程會讓膠料流動,於是殘留在胎圈上的小細毛就得拿刀片一一仔細地刮除。之後,還需再抽樣檢驗,如透過X光機檢查輪胎是否有缺陷,而且還要針對組成?胎的各個部裁進行取樣,並利用設備來驗證這些部裁的物理性是不是符合當初所設定的目標值。最後,再利用「走行試驗機」來檢查輪胎的高速性及荷重性能。當然,通過層層的檢測關卡後,就能為這條輪胎進行貼標,準備開始運送發貨。 |
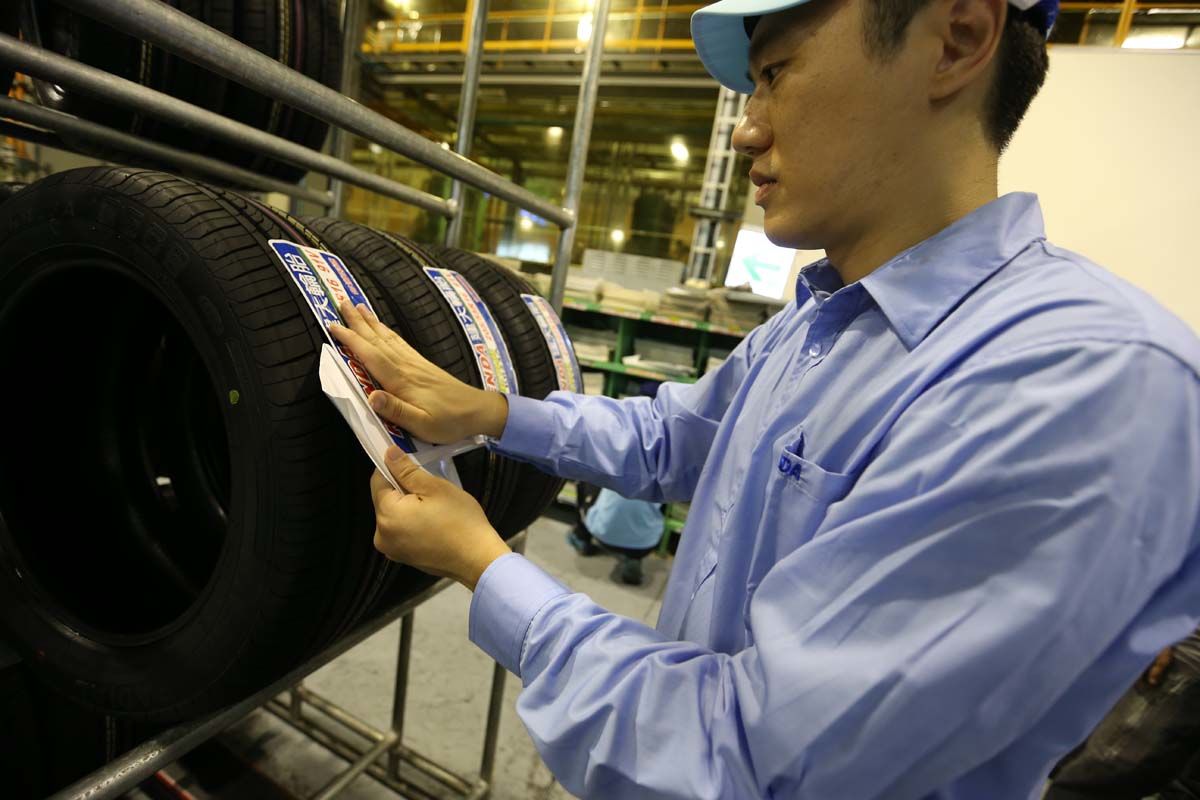 |
經過層層的檢查手續就可以安心地貼上產品標籤。 就是要嚴謹 其實在繁瑣、費工的輪胎製造過程背後,人不論在哪一個生產環節,都扮演著最為重要的角色。不論從備料、加工、組裝,甚至到檢驗,雖有機器的分憂解勞,但如果沒有人在其中來回的穿針引線,仔細地量測與檢查再檢查,那麼又何來能將一團團黑麻麻的膠料,轉變成一顆顆乘載人們安全移動的黑輪。在短短的一日體驗中,我雖然無法立馬成為一個技術純熟的輪胎製造員,但卻能深深感受到周遭廠內的每個人自眼神表露出那份對工作的態度是如此的認真與專注。所以,輪胎這門辛苦的產業不外乎要立基在嚴格的態度,才能製造出贏得消費者信賴的產品。 |
 |
掃描輪胎上的生產規格條碼,確認無誤便可進到標籤區準備出貨。 |